Product Overview
Item
|
Description
|
Product Name
|
Frequency Inverter/ AC Drive
|
Model Number
|
E5-H-4TxxG
|
Power Range
|
0.75kW-500kW
|
Rated Input Voltage
|
3 phase 380V/480V
|
Rated Output Voltage
|
3 phase 0 to rated input voltage
|
Input Frequency
|
50Hz/60Hz
|
Adaptable Motor
|
Asynchronous Motor
|
Control Mode
|
V/F Control, Vectorization V/F Control,
|
Communication
|
Modbus 485 RTU
|
IP Class
|
Standard IP20
|
Overload Capacity
|
150% 1 minute, 180% 10 seconds, 200% 0.5 second, interval: 10 minutes (inverse time lag feature)
|
Feature
■ Compact design for OEM customer requirements
■ Rich and flexible functions and customization functions meet various driving and speed regulation fields.
■ Parameter upload and download are realized in standard operation panel with copy progress indication, and uploaded parameters are selected to disable upload coverage.
■ With unique adaptive control technology, automatic current limiting and pressure limiting and underpressure suppression in operation.
■ Special parameter of constant pressure water supply,which has the function of sleep and wake.
■ Overload capacity is 150% 1 minute, 180% 10 seconds, 200% 0.5 seconds, with a 10-minute interval (inverse timing feature).
Model explanation
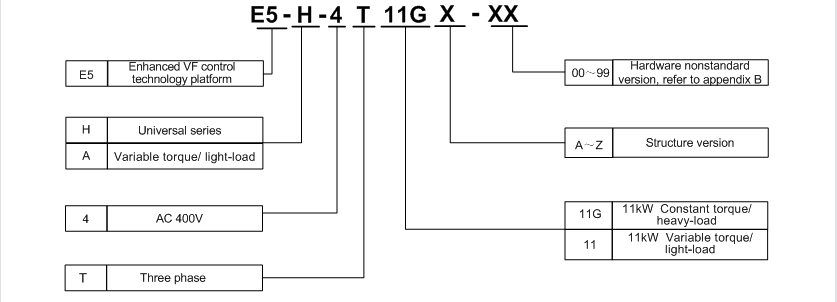
Product Catalogue
E5−H−4T□□□G Three−phase 400V Constant torque/heavy−duty application
Power (kW)
|
0.75
|
1.5
|
2.2
|
3.7
|
5.5
|
7.5
|
11
|
15
|
18.5
|
22
|
30
|
37
|
45
|
55
|
75
|
Motor
;power (kW)
|
0.75
|
1.5
|
2.2
|
3.7
|
5.5
|
7.5
|
11
|
15
|
18.5
|
22
|
30
|
37
|
45
|
55
|
75
|
Output
|
Voltage (V)
|
Three−phase 0 to rated input voltage
|
Rated current (A)
|
2.5
|
3.8
|
5.5
|
9
|
13
|
17
|
24
|
30
|
39
|
45
|
60
|
75
|
91
|
112
|
150
|
Overload capacity
|
150% ;1 minute, 180% ;10 seconds, 200% ;0.5 second, interval: 10 minutes (inverse time lag feature)
|
Input
|
Rated voltage/frequency
|
Three−phase 380V/480V; 50Hz/60Hz
|
Allowable voltage range
|
323V~ 528V; voltage imbalance ≤3%; allowable frequency fluctuation: ±5%
|
Rated current (A)
|
2.8
|
4.2
|
6.1
|
10
|
15
|
19
|
26
|
33
|
43
|
50
|
66
|
83
|
100
|
123
|
165
|
Braking unit
|
Built−in as standard
|
External braking unit
|
Protection class
|
IP20
|
Cooling mode
|
Natural air cooling
|
Force ;air cooling
|
Power (kW)
|
90
|
110
|
132
|
160
|
185
|
200
|
220
|
250
|
280
|
315
|
355
|
400
|
450
|
500
|
|
Motor ;
power (kW)
|
90
|
110
|
132
|
160
|
185
|
200
|
220
|
250
|
280
|
315
|
355
|
400
|
450
|
500
|
|
Output
|
Voltage (V)
|
Three−phase 0 to rated input voltage
|
Rated current (A)
|
176
|
210
|
253
|
304
|
350
|
380
|
426
|
470
|
520
|
600
|
650
|
690
|
775
|
860
|
|
Overload capacity
|
150% ;1 minute, 180% ;10 seconds, 200% ;0.5 second, interval: 10 minutes (inverse time lag feature)
|
Input
|
Rated voltage/frequency
|
Three−phase 380V/480V; 50Hz/60Hz
|
Allowable voltage range
|
323V ;~ ;528V; ;voltage ;imbalance ;≤3%; allowable frequency fluctuation: ±5%
|
Rated current (A)
|
No DC reactor
|
194
|
230
|
275
|
335
|
385
|
415
|
470
|
515
|
570
|
660
|
715
|
760
|
850
|
945
|
|
DC reactor*2
|
160
|
196
|
232
|
282
|
326
|
352
|
385
|
437
|
491
|
580
|
624
|
670
|
755
|
840
|
|
Braking unit
|
External braking unit
|
Protection class
|
IP20
|
Cooling mode
|
Force air cooling
|
If higher power level inverter is required, please contact the manufacture.
Note:
For 18.5kW to 75kW, the structure version is “A”, for other power class, the structure version doesn’t required to be shown for E5-H series.
Rated input current when external DC reactor is installed.
Technical Specification
Control characteristics
|
Control mode
|
Enhanced V/F control
|
Starting torque
|
0.50Hz 180%
|
Range of speed regulation
|
1:100
|
Precision of steady speed
|
± 0.5%
|
Product functions
|
Key functions
|
Under-voltage regulation, switchover of run command source(operation panel, terminal and communication), speed tracing function, multi− step frequency reference(up to 23 step frequency), motor data identification, S curve acceleration and deceleration, slip compensation, PID regulation, droop control, current limit, manual torque boost and auto torque boost, programmable digital inputs, programmable digital outputs
|
Frequency reference mode
|
Parameter setting, operation panel UP/DN, terminal, terminal UP/DN, communication, analog AI1, analog AI2,analog AI3, pulse DI, etc.
|
Frequency range
|
0.00 ~ 300.00Hz
|
Start frequency
|
0.00 ~ 60.00Hz
|
Acceleration time and deceleration time
|
0.1 ~ 36000s
|
Dynamic braking
|
Braking unit action voltage: 650 ~ 750V; operating time: 100.0s
|
DC braking
|
DC braking start frequency: 0.00 ~ 300.00Hz
DC braking current: constant torque: 0.0 ~ 120.0%
variable torque: 0.0 ~ 90.0%
DC braking time: 0.0 ~ 30.0s, DC braking function does not required waiting time to start to realize quick braking
|
Magnetic flux braking
|
Enabled or disabled during deceleration are optional, the default setting is enabled
|
Unique functions
|
Multi-function M key
|
The unique multi-function key can be set to frequently used operations: such as JOG, emergency stop, switchover of run command source, switchover of parameters display mode, etc.
|
Multiple parameter display modes
|
Basic parameters display mode, fast parameters display mode, non−factory setting parameters display mode, last changed 10 parameters display mode
|
Parameters copy
|
The standard operation panel can realize the parameters upload, download and display the copy progress. Users can set to forbid overwriting the uploaded parameters
|
Dual 485 communication ports
|
Dual 485 communication ports support Modbus protocol (RTU). The maximum distance is 500 meters
|
Operation panel
|
Key type or shuttle type operation panel are optional
Protection level: IP20 as standard, IP54 as option
|
Common DC bus
|
All series product support common DC bus
|
Independent duct
|
All series product adopts independent duct design and supports the installation of heat-sink outside the cabinet
|
Power-On-Self-Test
(POST)
|
Realizing the POST of internal and peripheral circuits, including motor grounded, abnormal +10V power supply output, analog input and disconnection, etc.
|
Protection function
|
Power supply under-voltage, over-current protection, over-voltage protection, interference protection, abnormal comparison level, motor data identification failure, module(IPM) protection, heat-sink over temperature protection, inverter overload protection, motor overload protection, peripheral protection, abnormal current detection, output short circuit to ground, interruption of power supply when in running status, abnormal input power, output phase loss, abnormal EEPROM protection, abnormal pre-charging contactor detection, temperature sampling disconnection, abnormal +10V power supply, abnormal analog input, motor over temperature protection(PTC), abnormal communication, abnormal software version compatibility, abnormal copying, terminal mutual exclusion detection, hardware overload protection
|
Efficiency
|
At rated power:
E5-H series: 7.5kW and below power class ≥93%
45kW and below power class ≥95%
55kW and above power class ≥98%
E5-A series: 55kW and below power class ≥95%
75kW and above power class ≥98%
|
Environment
|
Operating site
|
The product should be mounted vertically in the electric control cabinet with good ventilation. Horizontal or other installation modes are not allowed. The cooling medium is the air. The product should be installed in the environment without dust, corrosive gas, combustible gas, oil mist, steam, drip and free from direct sunlight
|
Ambient temperature
|
−10 to +40ºC, the product must be de-rated rated output current for the ambient temperature between 40ºC to 50ºC, the rated output current must be de-rated for 1% per 1ºC temperature rise
|
Humidity
|
5 to 95%, no condensing
|
Altitude
|
0 to 2000m, the product must be de-rated rated output current for the altitude above 1000 meters, the rated output current must be de-rated for 1% per 100 meters rise
|
Vibration
|
3.5m/s2,2 to 9Hz; 10 m/s2,9 to 200Hz; 15 m/s2,200 to 500Hz
|
Storage temperature
|
−40 to +70ºC
|
Motor Wiring
It is forbidden to short circuit the speed control inverter output terminals or short circuit to ground, otherwise the internal components of the variable frequency inverter will be damaged.
Do not short circuit the output cable to the 3 phase frequency drive enclosure, otherwise electric shock may happen.
It is forbidden to connect the output terminal of the inverter to the capacitor or LC/RC noise filter with phase lead, otherwise, the internal components of the inverter may be damaged.
When contactor is installed between the inverter and motor, it is forbidden to switch on/off the contactor when the VFDs is running; otherwise, large current will flow into the industrial inverter, triggering the inverter protection action.
Length of cable between the inverter drive and motor. If the cable between the frequency inverter and the motor is too long, the high−order harmonic leakage current of the output end will cause adverse impact on the AC inverter and the peripheral devices. Output AC reactor should be installed if the motor cable is longer than 100m, Refer to the following table for the switching frequency setting.
Length of cable between inverter and motor
|
≤ 50m
|
≤ 100 m
|
> 100m
|
Switching frequency (PA.00)
|
< 15kHz
|
< 10kHz
|
< 5kHz
|
Installation Dimension
E5−H−4T7.5G ;And below ;power class
E5−H−4T11G ; ;And ;above ;power class
Product appearance, Installation dimension, Approximate weight
Voltage
|
Model
|
Appearance and Installation Dimension(mm)
|
weight(kg)
|
W
|
H
|
D
|
W1
|
H1
|
D1
|
T1
|
Hole ;d
|
400V
|
E5−H−4T0.75G
|
118
|
190
|
155
|
105
|
173
|
40.8
|
3
|
5.5
|
1.5
|
E5−H−4T1.5G
|
118
|
190
|
175
|
105
|
173
|
60.5
|
4
|
5.5
|
2.6
|
E5−H−4T2.2G
|
E5−H−4T3.7G
|
E5−H−4T5.5G
|
155
|
249
|
185
|
136
|
232
|
69
|
8
|
5.5
|
4.5
|
E5−H−4T7.5G
|
E5−H−4T11G
|
210
|
337
|
200
|
150
|
324
|
88
|
2
|
7
|
8.5
|
E5−H−4T15G
|
E5−H−4T18.5G
|
289
|
440
|
215
|
200
|
425
|
88
|
2.5
|
7
|
17
|
E5−H−4T22G
|
E5−H−4T30G
|
E5−H−4T37G
|
319
|
575
|
212
|
220
|
553
|
90.5
|
2.5
|
10
|
25
|
E5−H−4T45G
|
E5−H−4T55G
|
404
|
615
|
255
|
270
|
590
|
86.5
|
3.0
|
10
|
35
|
E5−H−4T75G
|
E5−H−4T90G
|
465
|
745
|
325
|
343
|
715
|
151.5
|
3.0
|
12
|
55
|
E5−H−4T110G
|
E5−H−4T132G
|
540
|
890
|
385
|
370
|
855
|
205.5
|
4.0
|
14
|
85
|
E5−H−4T160G
|
E5−H−4T185G
|
E5−H−4T200G
|
E5−H−4T220G
|
700
|
1010
|
385
|
520
|
977
|
210
|
4.0
|
14
|
125
|
E5−H−4T250G
|
E5−H−4T280G
|
E5−H−4T315G
|
810
|
1358
|
425
|
520
|
1300
|
210
|
4.0
|
14
|
215
|
E5−H−4T355G
|
E5−H−4T400G
|
E5−H−4T450G
|
E5−H−4T500G
|
Applications
Variable Frequency Drive Representative Industry
The use of variable frequency drive (VFD): a VFD is used to regulate the speed and torque of the Motor according to the variation of the load in order to improve the Motor energy efficiency. The High Performance Universal Inverter of Shenzhen V&T Technologies Co.,Ltd. is suitable for Air Compressor Industry, Textile Industry, Crane and Lifting Industry, Chemical Industry, Mining Machinery Industry, Ceramic Machine Industry, Injection Molding Industry, Die casting machine industry, Transport Machinery Industry, Stone processing industry, Fan&Pump Industry, Building Materials Industry, Packaging Machinery Industry, Food Machinery Industry, Wood-working Machinery Industry , Machine Tool Industry, Metal Processing Industry, Oilfield and Petroleum Industry, Printing and Packing Industry, Tension Control Industry and other simple applications of speed regulation.