Product Description
PDCPD is a highly reactive, high-performance liquid resin, consisting of A and B bi-components. PDCPD is a remarkable environmentally friendly new material in the world today, and is recognized as a "model of green chemistry.”
A MATERIAL COMPOSITION
|
|
B MATERIAL COMPOSITION
|
Chemical Name
|
In% By Weight
|
CAS No.
|
|
Chemical Name
|
In% By Weight
|
CAS No.
|
Dicyclopentadiene
|
80-90%
|
77-73-6
|
|
Dicyclopentadiene
|
80-90%
|
77-73-6
|
Cyclopentadiene trimer
|
5-10%
|
7158-25-0
|
|
Cyclopentadiene trimer
|
5-10%
|
7158-25-0
|
Tackifier
|
0-5%
|
Mixed
|
|
Tackifier
|
0-5%
|
Mixed
|
Alkyl aluminum compounds
|
≤1.8%
|
Mixed
|
|
Alkyl aluminum compounds
|
≤1.0%
|
Mixed
|
Silicone oil
|
≤0.05%
|
9006-65-9
|
|
Silicone oil
|
≤0.05%
|
1333-86-4
|
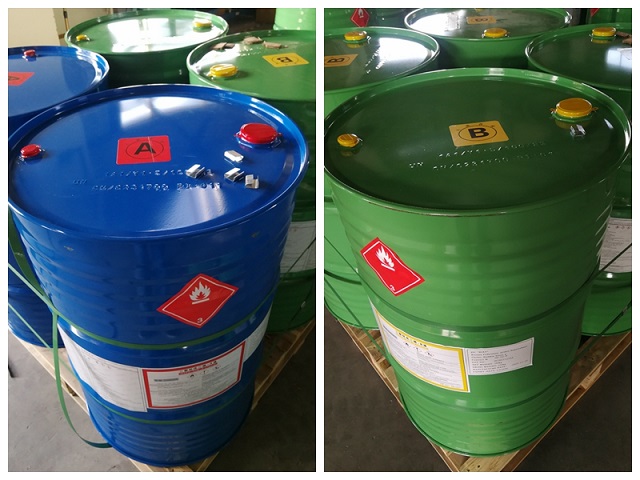
A WIDE RANGE OF PDCPD APPLICATION
PDCPD is most suitable for the manufacture of construction machinery, agricultural machinery, trucks, automobile coverings, integrated large-scale molding products represented by sanitary equipment, and purification tanks. It is the ideal material to replace glass fiber reinforced plastic, some plastics, metal sheet metal parts, carbon fiber, and alloy in the future, and it is also the high-quality choice for lightweight equipment in many new industries such as new energy automobile, wind power generation, unmanned aerial vehicle, tunnel template, robot and so on, and the application field is extremely broad, and it can be widely used in the fields of automobile manufacturing, construction engineering template, agricultural machinery, military, civil, medical, scientific research and national defense, and it has great market potential and development space. development space is huge.
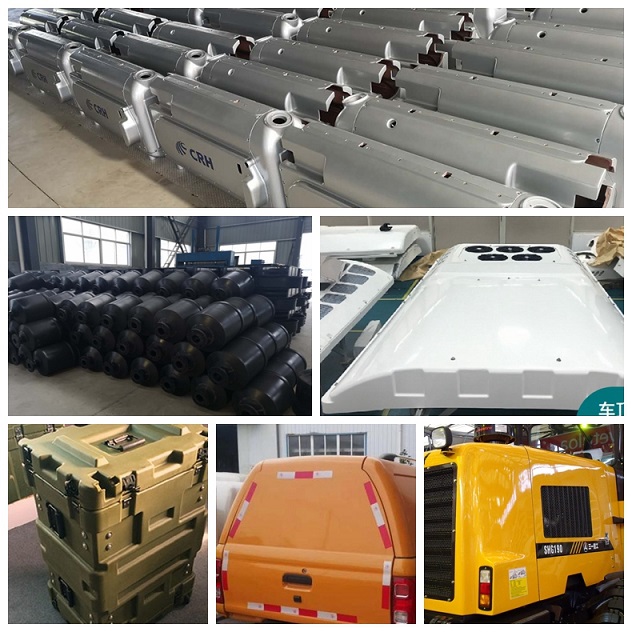

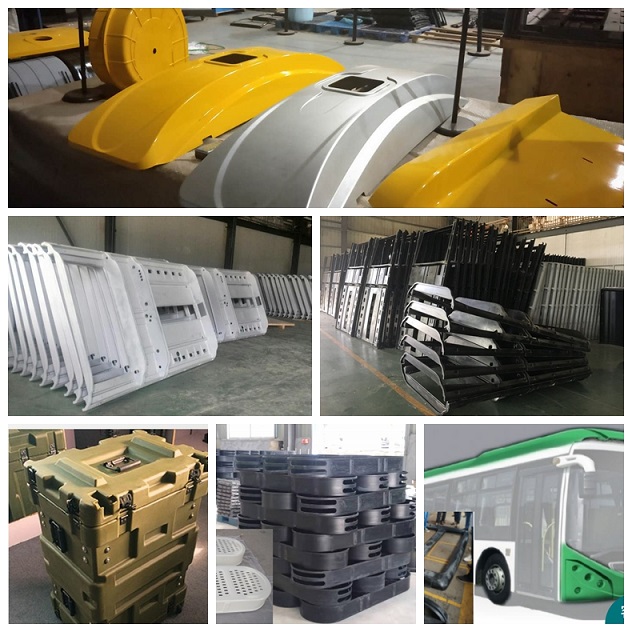
PDCPD Products High Properties Test Reference
Content
|
Unit
|
Testing Method
|
Content
|
Unit
|
Testing Method
|
Tensile strength
|
47.5MPa
|
GB/T 1040.2-2006
|
Rockwell hardness
|
115
|
GB/T3398.2-2008
|
Tensile modulus
|
1900MPa
|
GB/T 1040.2-2006
|
Distortion temperature
|
110.5
|
GB/T1634.2-2004
|
Elongation at break
|
12.30%
|
GB/T 1040.2-2006
|
Density
|
1.03g/cm³
|
GB/T1033.1-2008
|
Compressive strength
|
60.8MPa
|
GB/T 1041-2008
|
Glass transition temperature
|
169℃
|
GB/T19466.2-2004
|
Bending strength
|
75.6MPa
|
GB/T9341-2008
|
Burning horizontally
|
HB40
|
GB/T2408-2008
|
Bending modulus of elasticity
|
2053MPa
|
GB/T9341-2008
|
Water Absorption
|
0.10%
|
GB/T1034-2008
|
Notched impact strength
of cantilever beam (23℃)
|
33.1
|
GB/T1843-2008
|
Automotive interior combustion
Performance (burning rate)
|
A-0
|
GB 8410-2006
|
Notched impact strength of
cantilever beam (-40℃)
|
12.8
|
GB/T1843-2008
|
Rockwell hardness
|
115
|
GB/T3398.2-2008
|
Ten Advantages of PDCPD Products Properties
1. Wide molding range: two-component, low-viscosity liquid resin injection molding, shape, runner, and pressure restrictions are small, can produce large, complex shapes, the wall thickness of the workpiece.
2. Equipment Investment: simple molding process, low pressure and temperature requirements, less investment in molding equipment, low mold costs, long service life of the mold, small amortization costs
3. Good balance of physical properties: excellent and balanced physical properties, especially the combination of high impact resistance and high rigidity, can get lightweight, high strength, rugged, and durable parts.
4. Temperature and corrosion resistance: outstanding resistance to temperature change, high temperature does not creep, low temperature does not cause brittle crack, can be used in -40 ~ 100 ℃ environment for a long time: excellent corrosion resistance, especially acid resistance, alkali resistance is outstanding.
5. High product precision: the product deformation is small, the size error is small, and the consistency of the workpiece is high; in general, the control of the size error of the workpiece can reach the GB/T1804-m level.
6. Excellent decorative properties: the surface of the molded parts is easy to form a dense oxide film with good adhesion to paint. It can also be plated, water transfer printing, and other surface decorative treatments.
7. Good designability: high degree of design freedom, can be pre-embedded, riveted, glued, self-tapping, and drilling, can be unequal thickness structure, sandwich structure, composite structure, etc.
8. High molding efficiency: short mold development cycle. Less production labor, high molding efficiency, product molding cycle is generally 3 ~ 5 min. can be configured with robot to achieve automated demolding, trimming, and so on.
9. Good Safety and environmental protection: no fiber and dust, no poison and pollution, less edge residue, recyclable and harmless reuse, reuse more ways, high added value.
10. Wide range of applications, design freedom, applied in various automobiles, engineering equipment, medical equipment, chemical equipment, entertainment facilities, military, civilian, and other fields. Excellent performance, PDCPD material process, green, lightweight, high strength, green, fast and economical industrial closure.
Packing and Delivery
Packing:Metal Barrel, Net Weight:195kg/barrel; Gross Weight:220kgs/barrel
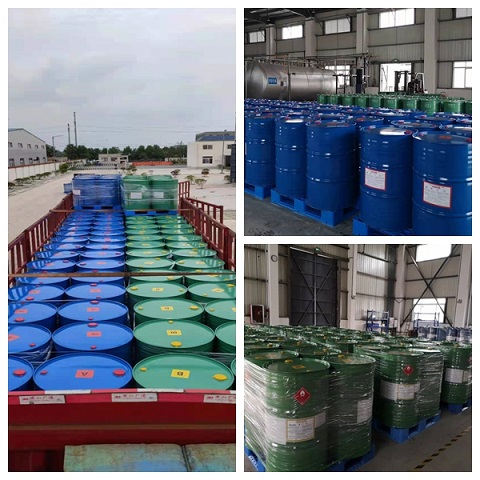
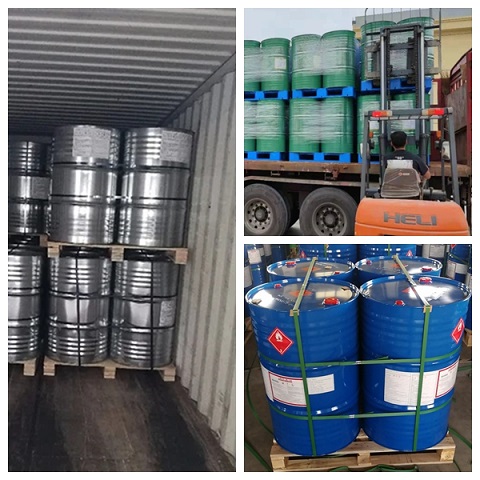
Outstanding Features of PDCPD MATERIAL
Safe Flame Retarant
PDCPD material has reached UL94-HB grade. The central flame retardant mechanism is: that the catalyst promotes the surface carbonization and air insulation flame retardant. Its unique flame retardant safety performance:
During passive combustion, the release of harmful fumes is low, comparable to the release of non-flame retardant general-purpose polypropylene plastics. Compared with traditional flame retardant materials, it dramatically reduces the risk of injury to people at the scene of a fire (the proportion of deaths caused by toxic fumes in a fire is high).
There are no heavy metals or toxic substances left in the combustion process, which will not cause pollution to the environment. It belongs to thermosetting material, does not produce melting drops, flame retardant anti-melting drops.
Green and Sustainable
Complies with occupational health requirements. The material meets the requirements of the international "Banned Substances Program" and does not contain any of the substances listed in the RoHS and REACH SVHC lists. Burning does not produce toxic or hazardous substances.。
It is a model material for energy saving and emission reduction. All the production process of this material has low energy consumption and low emission. The total energy consumption of the whole production process is <5000kcal/kg, which is about 1/2 of the energy consumption of polypropylene production.
It’s completely harmless and can be recycled。
① Its low-temperature anaerobic cracking can generate light fuel oil and carbon black, and it is efficient and convenient for a wide range of applications.;
② Its low-temperature anaerobic catalytic cracking generates C4 alkane fuel gas and carbon black;
③ it can be recycled and crushed as pavement asphalt as well as thermo-compression plastic modified reinforcing filler;
④ also, as a high-energy fuel, it can be supplied for garbage power plants, combustion calorific value = 1.5 times the standard coal.