Automated molding production line mainly consists of molding machine,casting line,cooling line,transport system,electronic control,hydraulic pressure and pneumatic system.
MAIN TECH.SPEC:
Model
|
JN6171
|
Sand size(mm)long(L)×wdith(B)
|
610×710
|
Modeling method
|
Start blowing sand+squeeze
|
Modeling speed (excluding core length)
|
30 seconds/floor
|
Compressed air consumptio
|
1.3m³
|
System air pressure
|
0.8Mpa
|
Using voltage
|
AC220V orAC380V
|
Using motor power
|
18kw
|
Hydraulic system,maximum pressure
|
6Mpa
|
Sand type weight
|
250kg
|
Automated molding production line features:
1)Horizontal classification, vertical sand shooting, horizontal casting
The sand is sanded from the vertical direction and has the best filling performance, which completely improves the shadow defects that may be generated by horizontal sand shooting. The “horizontal type, vertical shot sand, horizontal casting” process is simple, the model and sprue layout are convenient, the process yield is high, and the product adaptability is wider.
2)Mold height, compaction pressure adjustable
Users can flexibly choose the mold height and compaction pressure under different castings to ensure the reasonable use of sand.
3)Template replacement is convenient
Template installation: Four screws are fixed and replaced within five minutes to accommodate frequent mold changes.
4)Fault display
With the touch screen fault display, when a fault occurs, the cause of the fault is displayed on the touch screen, and the user can easily find the fault and take action.
5)Hydraulic, pneumatic, electrical system reliability
Hydraulic, pneumatic and electrical parts are all imported components to ensure stable and reliable operation of the equipment and service life.
6)The core is easier, more secure, more secure
The various types of equipment produced by the company use a stable and reliable security defense system.
7)Using servo hydraulic system, more energy efficient
With the servo hydraulic system, the supply pressure of the system can be automatically adjusted in real time according to the various stages of equipment operation, reducing energy loss.
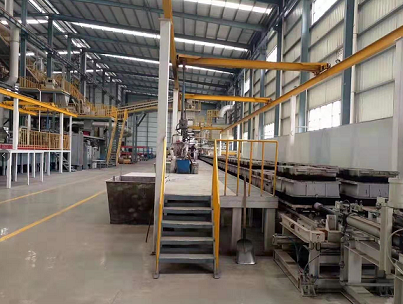
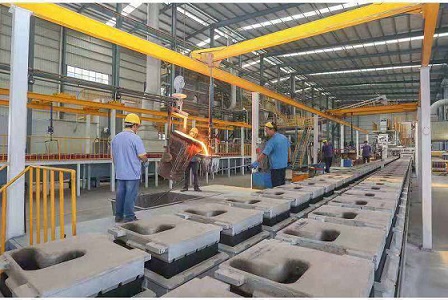