BENTLY NEVAD 133442-01 I/O Module with Internal Terminations
3500/50M 133442-01 Tachometer Module can be configured to supplyconditioned Keyphasor signals to the backplane of the 3500 rack for useby other monitors. Therefore, you don't need a separate Keyphasormodule in the rack.
|
133442-01 Datasheet
|
Signal Each 3500/50M TachometerModule accepts up to twotransducer signals from proximityprobe transducers or magneticpickups.
|
Input signal range +10.0 V to -24.0 VSignals exceeding this range arelimited internally by the module
|
Input impedance 20 k Ω (standard)40 k Ω (TMR)7.15 k Ω (Internal Barrier)
|
Parts delivered worldwide
|
Award-winning service
|
More than 25 in stock
|
Full 12-month warranty
|
We deliver worldwide
|
133442-01 is a Tachometer I/O Module with Internal Terminals manufactured and designed by Bently Nevada as part of the 3500 Series used for machinery vibration monitoring systems. Each 3500/50M Tachometer Module accepts up to two transducer signals from proximity probe transducers or magnetic pickups. Signals exceeding this range are limited internally by the module. The 3500/50M Tachometer Module supports 1 to 255 events per revolution for Rotor Acceleration and Zero Speed channel types. All other channel types support 0.0039 to 255 events per revolution. All channel types support a maximum full-scale range of 99,999 rpm and a maximum input frequency of 20 kHz. The minimum input frequency for proximity transducers is 0.0167 Hz (1 rpm for 1 event per revolution). The minimum input frequency for passive magnetic pickups is 3.3 Hz.
FUNCTIONS OF I/O MODULE:
It interfaces with sensors like tachometers, magnetic pickups, or encoders to monitor the speed of rotating machinery such as turbines, motors, or generators. Featuring internal terminals, the module simplifies wiring, improves reliability, and reduces installation complexity.
It processes various input signals, including analog, digital, or pulse-based formats, and provides outputs compatible with control systems through digital signals, analog outputs, or communication protocols like Modbus or CAN. With advanced signal conditioning and diagnostic capabilities.
It ensures accurate speed measurement and fault detection, making it essential for applications in turbine control, industrial automation, and power generation. Ruggedly designed to endure harsh environments, these modules seamlessly integrate with PLCs, DCS, or SCADA systems, ensuring precise control and monitoring for critical operations.
The module receives input signals from speed sensors, such as tachometers, encoders, or magnetic pickups. These signals could be in the form of analog voltages, digital pulses, or frequency-based signals.
Incoming signals are filtered, amplified, and normalized by the module's internal circuits to remove noise and ensure accurate processing. This step adapts raw sensor data to the module's required format for analysis.
sales7@amikon.cn
86-18965423501
86-18965423501
AMKPLC 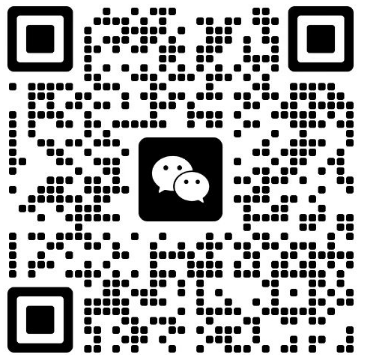