Item No
|
SS6159 Golden Black
|
Materials
|
High purity 93% natural quartz powder, 7%
unsaturated polyester resin and small amount of pigment .
|
Size
|
3000x1400mm,3000x1600mm, 3200x1400mm,3200x1600mm
etc.
|
Thickness
|
12mm,15 mm, 18 mm, 20 mm, 30 mm
|
Finish
|
Polished, Honed,etc.
|
Harness
|
7 Mohs
|
Water Absorption
|
≤0.04%
|
Ideal Use
|
Kitchen counter tops,bathroom vanity top, shower
stalls, wall tile, wall cladding, floor tile,etc.
|
MOQ
|
100square Meter
|
Quality control
|
Color difference control,Safe packing,
Thickness tolerance:+/-1mm
All products are checked by experienced QC piece by
piece and then pack
|
Packing
|
Packed with strong wooden crates and foam, film
inside
|
Unlike natural stone
slabs, quartz is an engineered product. Its primary ingredient, ground quartz,
is combined with polyester resin to create a binding — which makes it stain and
scratch resistant,heat resistance, corrosion resistance. Like granite or
marble, you have to consider it as an investment in your home, but quartz’s
durability and ease of maintenance means that your investment will be a lasting
one.
Engineered quartz
countertops is not porous and is made with resin mixed with
ground quartz, it do not need to be sealed. During your cleaning, there will be no need to take special measures,
instead all that is required is for you to use a wet cloth and mild soap. There
will also be no chance of the Quartz countertops harbouring any bacteria or
holding onto any spillages too. Just be sure to use natural stone cleaners
since quartz is mostly natural stone these cleaners are optimum for cleaning
quartz as well.
The Production Process:
1.
The process begins with a strict inspection of raw materials.
2.
The natural quartz raw material and polymer resins and inorganic pigments are
put into the mixers and mix together.
3.
After mixing, pour them into a mold and form them into slab size.
4.
Pressing: Then the slab is compacted by a special vacuum and vibration process
at pressure machine.
5.
Then the slab is moved to the curing kiln and heated for a period time to make
their final strenth and srurdiness.
6.
Cut edges, flat , thicknessing and polishing surface to perfect finished.
7.
Finally, through quality inspection and plastic film packaging.
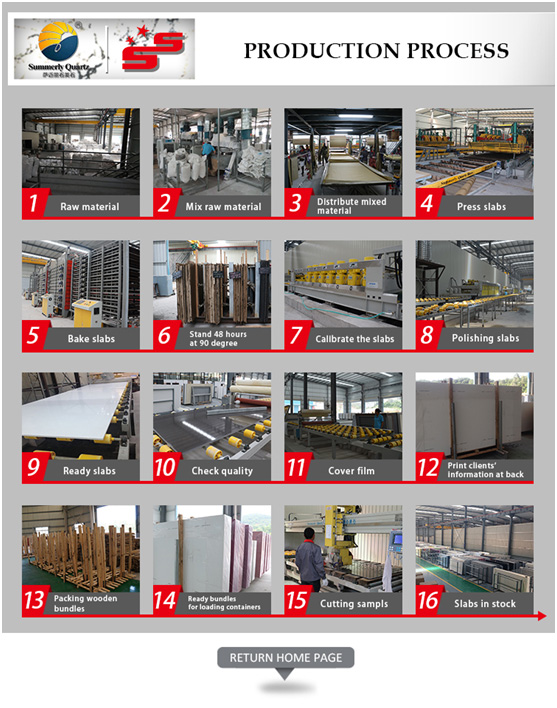
Sample Room:
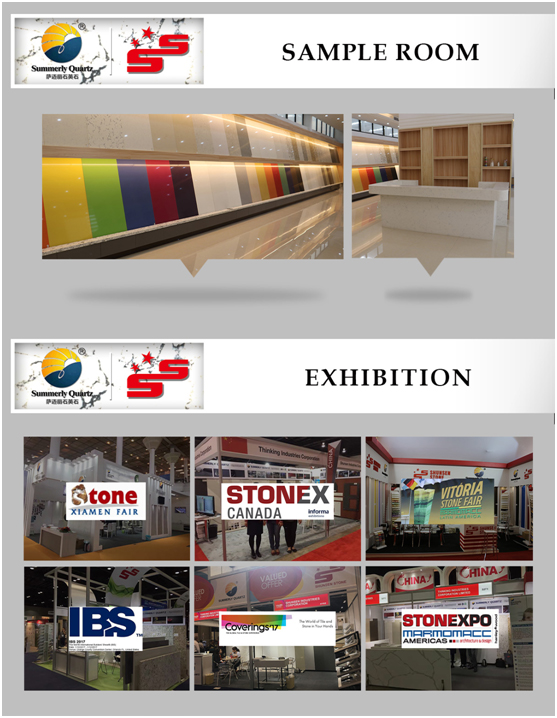