Item No
|
SS6313 Cararra
|
Size
|
3000x1400mm,3000x1600mm, 3200x1400mm, 3200x1600mm etc.
|
Thickness
|
12 mm, 15 mm, 18 mm, 20 mm, 30 mm
|
Tone & Figure
|
Consistent
|
Density
|
2.3~2.5g/cm3
|
Flexural Strength
|
25~35Mpa
|
Ideal Use
|
Kitchen counter tops, kitchen worktops, table tops,bench top, island tops,back splash, shower stalls, etc.
|
Quality control
|
Every slab will be checked very carefully at least twice according to customers' requests.
|
Packing
|
Plastic inside strong seaworthy wooden bundle outside
|
MOQ
|
100square Meter
|
OEM
|
Yes
|
Quartz is a mineral found in the earth’s continental crust, and is one of the most abundant and strongest materials on the planet. Quartz is a manufactured surface that is made by mixing ground natural quartz with polymer resins. Quartz is an extremely versatile material, which can be tinted, treated or shaped to accommodate almost any homeowner's tastes.Quartz is as tough as granite–but there are a few differences between these materials as well. The polymers and resins used to make quartz countertops make them absolutely nonporous, which means they’re stain-resistant.
Maintenance is a key factor in any kitchen because you need it to be fast and simple so that you can get on with your busy day. The good news here is that quartz countertops require very little maintenance and you do not have to seal it or use specialty cleaners. Quartz is not nearly as sensitive as marble.You simply don't know which cleaner may be the one to stain your quartz so sticking to granite cleaners and other products formulated for use around natural stone is the safe bet.
The Production Process:
1. The process begins with a strict inspection of raw materials.
2. The natural quartz raw material and polymer resins and inorganic pigments are put into the mixers and mix together.
3. After mixing, pour them into a mold and form them into slab size.
4. Pressing: Then the slab is compacted by a special vacuum and vibration process at pressure machine.
5. Then the slab is moved to the curing kiln and heated for a period time to make their final strenth and srurdiness.
6. Cut edges, flat , thicknessing and polishing surface to perfect finished.
7. Finally, through quality inspection and plastic film packaging .
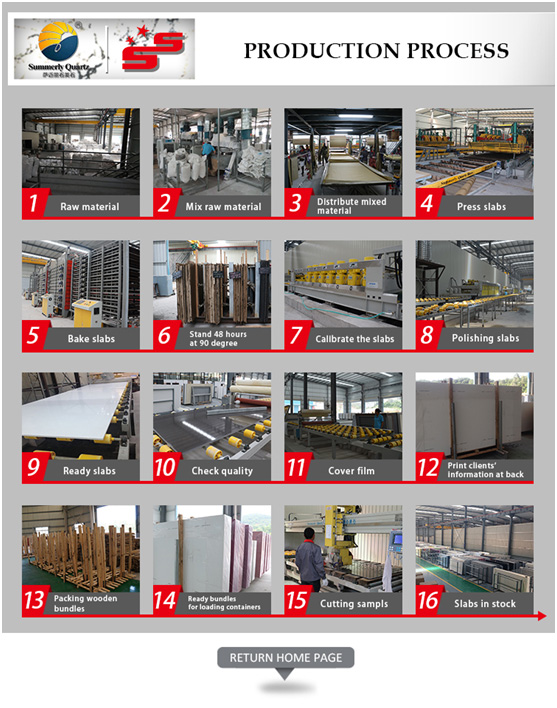