CNC lathe machine
Main features:
1. High precision spindle unit
The CAK5085A CNC lathe using self-developed spindle unit head,the bearing match front-three and after-two bearing,has high speed, high rigidity, low noise, long lasting precision,the Spindle beat rate is less than 3um.
2. CNC lathe machine body adopts high rigidity cast iron with resin sand technics,it has compact structure ,smooth chip remover, attractive appearance.
3. Tool test form
The min.repeat tool changing error of new servo tool turret is ±3um,the tool changing speed is high and accurate,can save working time greatly.
4. High precision feed
Each feed spindle is fully servo driver,adopts Yaskawa(Japan) driver and motor,PMI(Taiwan) liner guide way,to keep long time working precision.The repeat positioning accuracy is less than ±3um.
5. High efficiency machining
The spindle Max. speed is 5000rpm/min,X Axis rapid moved can reach to 18
meters/min, Z Axis rapid moved can reach to 20 meters/min. High precision hydraulic rotary cylinder,Taiwan precision chuck,improve the ability of ductile material cutting and strong cutting.
6. Strong Cooling
High power strong cooling pump, greatly improved the parts cutting, according to customer requirements can be installed 1--4 cooling pipe, cooling performance is good.
Main structure
This CNC lathe machine mainly composed by machine body,tool rest,Spindle cabinet,a nd equipped with an independent electrical cabinet, centralized lubrication device, high protective cover.
1. Body
The Body adopts integrated casting body with high quality, trough manual tempering and aging treatment by three times. The surface of the guide way is treated by super audio quenching, the structure is reasonable,to ensure rigidity, precision and the stability of the machine.
2. Tool rest
Each feed spindle is fully servo driver,adopts Yaskawa(Japan) driver and motor,PMI(Taiwan) liner guide way,to keep long time working precision.The repeat positioning accuracy is less than ±3um.
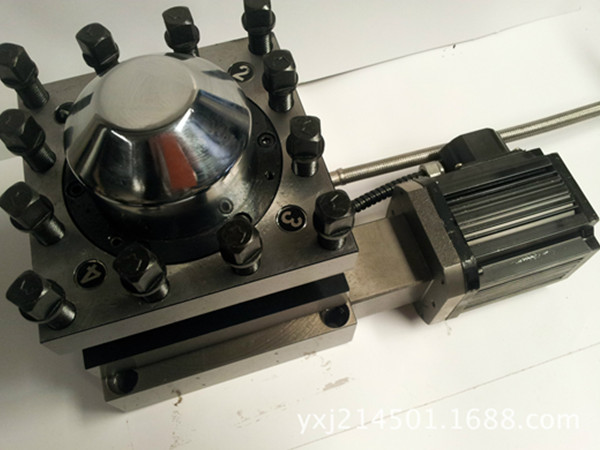
3. High precision spindle unit
The CAK5085A CNC lathe using self-developed spindle unit head,the bearing match front-three and after-two bearing,has high speed, high rigidity, low noise, long lasting precision,the Spindle beat rate is less than 3um.
4. Electrical cabinet
The Electrical cabinet is independent and closed.Installed with CNC controller, Inverter and electrical components.Also set air cooling device to ensure that the electrical components of the machine work properly, no dust.
Multifunction CNC Controller
This product is a high-quality CNC device with all digital bus.It keeps abreast with overseas high-grade CNC Controller,adopts upper and lower machine structure using double CPU module, modular and open architecture,based on NCUC industrial fieldbus technology with independent intellectual property rights. It has the functions of multi channel control technology, five axis machining, high speed and high precision, turning milling compound and synchronous control, using 15 'LED LCD screen. Mainly used in high speed, high precision, multi axis, multi channel vertical, horizontal machining center, turning milling compound, 5 axis gantry machine tools, etc..
Item
|
Unit
|
Data
|
Remark
|
Machine/pallet Max.turning diameter
|
mm
|
420/360
|
|
Workpiece Max.turning diameter of skateboard
|
mm
|
230
|
|
Body guide way width
|
mm
|
350
|
|
Center distance
|
mm
|
750
|
750machine
|
1000
|
1000machine
|
Effective working length(4/6 workstation)
|
mm
|
650/580
|
750machine
|
900/830
|
1000machine
|
Max.turning diameter
|
Vertical four workstation
|
mm
|
365
|
|
Horizontal six workstation
|
mm
|
270
|
|
X Axis travel
|
mm
|
220
|
|
Z Axis travel
|
mm
|
750
|
750machine
|
1000
|
1000machine
|
X/Z rapid moving speed
|
mm/min
|
6/8(8/10) optional
|
|
X axis servo motor torque
|
Nm
|
4
|
GSK 980TC3
|
7
|
FANUC 0i TD
|
5
|
HNC180XP-T3/
HNC808B
|
Z axis servo motor torque
|
Nm
|
6
|
GSK 980TC3
|
11
|
FANUC 0i TD
|
7.7
|
HNC180XP-T3/
HNC808B
|
Spindle speed range
|
rpm
|
100-2500/3500optional
|
|
Spindle head type
|
type
|
A2-6
|
|
Spindle hole diameter and inner hole taper
|
type
|
Ø66mm
|
|
Ø70mm 1:20
|
|
Manual chuck and through hole
|
mm
|
Ø200/66
|
|
Hydraulic three jaw chuck and through hole
|
mm
|
3H-08A6(Ø36)
|
|
Spindle motor power
|
kw
|
5.5 servo(standard)/7.5 servo (optional)
|
|
Automatic Tool rest form
|
type
|
4 station vertical (optional 6 Station horizontal)
|
|
Tool specifications
|
mm
|
25x25
|
|
Tailstock sleeve diameter /Travel
|
mm
|
Ø60/120
|
|
Taper of tailstock sleeve hole
|
mm
|
MT-#4
|
|
Working accuracy
|
mm
|
IT6
|
|
Repeat positioning accuracy
|
mm
|
X:0.012;Z:0.016
|
|
Roughness
|
um
|
Ra≤1.6
|
|
Machine size
|
m
|
2.35x1.6
|
|
Packing dimensions
|
m
|
2.7x1.9x2.1
|
|
NET weight/Gross weight
|
t
|
1.8/2.1
|
|
CNC controler
|
CNC 818(Standard)
HNC/FANUC/SIEMENS(optional)
|
|
After service
1. Ensure the equipment package meets the requirements of moisture, rain, rust, anticorrosion and shockproof, the mark is clear and correct, make the goods safe, timely delivery to the site.
2. High-quality and fast technical service
In order to better ensure the normal operation of the equipment, timely answer user questions, help users solve problems, the company special maintenance center. Responsible for equipment maintenance and technical consulting services. The maintenance center is responsible for providing free technical consulting services to customers at any time.
3. free debugging for users, open
The engineer shall be responsible for the installation, commissioning, opening and testing of on-site equipment. After the equipment has been successfully debugged, the supplier shall provide the test results in writing to the user, and the supplier's technical personnel may withdraw from the site only with the consent of the user.
4. Regular inspection
Our company sets the inspection system as one of the routine maintenance work, that is, the company organizes the equipment inspection once every six months. With the participation of designers, and listen to the user response to the problems and suggestions, constantly improve the software and hardware functions and quality of the product.
5, quality guarantee period
Warranty period: the warranty period of equipment under the contract is 12 months after the successful installation and commissioning. The cost of spare parts (except force majeure factor and artificial damage) is borne by the supplier during the warranty period.
6. lifelong maintenance to ensure the interests of users
Huadian CNC equipment Manufacturing Co., Ltd. Equipment from the date of acceptance, normal conditions (in addition to force majeure factors and artificial damage, free warranty for 12 months. Warranty expires. The company continues to provide lifetime free service, if you need to replace spare parts, only charge cost.
7. Establish user files and improve product quality
In addition to carrying out customer technical consulting service, the company maintenance center is also responsible for receiving and collecting customer complaints and consulting information to ensure that the questions and requests raised by users can be dealt with in a timely manner. And to track and verify the handling situation. At the same time to establish user records of the use of products to provide the basis for future product quality improvement. We will continue to strive to improve. To provide customers with the most satisfactory products and services.
8. Spare parts reserve and mode of supply
Our company reserves all kinds of equipment fittings for a long time, can choose express delivery, china railway express, air transportation, road distribution and so on according to the request of the user. The emergency spare parts can be transported to the user's scene within 24 hours
9. Technology upgrade service
Our company provides the software upgrade version free of charge to the user. When we need to change the PLC program or the computer program due to the special requirements of the user and the process change, we are responsible for the change and will not charge for the software.
If you are interested in our brass spindle making machine,please contact us!