What is CNC Machining(The definition of CNC Machining)
CNC (Computer Numerical Control) machining is a manufacturing process that uses computerized controls and machine tools to produce complex and precise parts and components. It involves the use of computer-aided design (CAD) software to design the part and convert the design into a code (G-code) that can be read by the CNC machine.
The CNC machine then uses the G-code to control the movement of cutting tools or other tools, such as drills or lathes, to remove material from the raw material (such as metal or plastic) to create the desired shape and dimensions. CNC machines can produce parts with high precision and accuracy, and they can be programmed to produce identical parts in large quantities. CNC machining is used in a variety of industries, including aerospace, automotive, medical, and electronics.
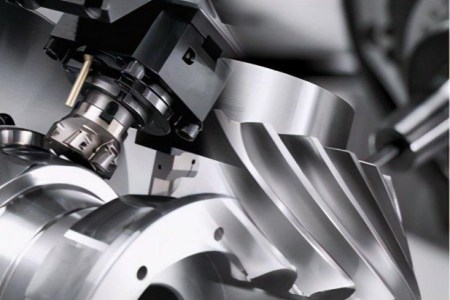
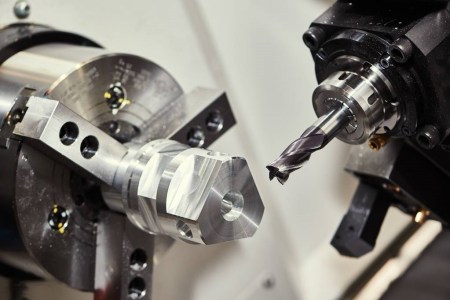
Advantages of CNC Machining
CNC (Computer Numerical Control) machining offers several advantages over traditional manufacturing methods. Some of the key advantages of CNC machining include:
• Precision and Accuracy:
CNC machines can produce parts with high precision and accuracy, making them ideal for creating complex shapes and parts with tight tolerances.
• Consistency:
CNC machines can produce identical parts in large quantities with consistent quality, reducing the chances of errors and variations in the final product.
• Automation:
CNC machines are fully automated, which means that they can run for long periods without human intervention. This reduces the need for manual labor and increases efficiency and productivity.
• Flexibility:
CNC machines can be programmed to produce a wide range of parts and components, making them ideal for prototyping and small production runs.
• Reduced Waste:
CNC machines are capable of producing parts with minimal waste, as they can be programmed to optimize material usage and reduce scrap.
• Faster Turnaround Time:
CNC machines can produce parts much faster than traditional manufacturing methods, reducing lead times and allowing for faster product development.
• Improved Safety:
CNC machines are designed to operate in a safe and controlled manner, reducing the risk of accidents and injuries in the workplace.
CNC Machining Processes:
CNC Milling:
CNC milling is a type of subtractive manufacturing technique that employs computer numerical control (CNC) to operate 3-axis and 5-axis cutting tools that remove material from plastic or metal blocks.
We employ both 3-axis milling and 5-axis indexed milling techniques to fabricate bespoke prototypes and end-use production components in as little as three days, using over 25 engineering-grade metals and plastics.
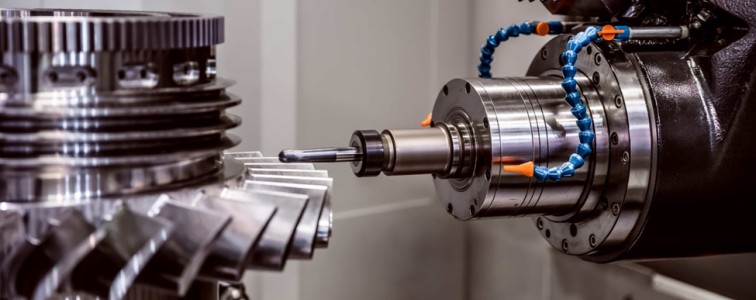

CNC Turning:
CNC turning is a highly precise form of machining that involves the removal of material by a cutting tool in contact with a rotating workpiece. The movements of the machinery are guided by computerized instructions, ensuring exceptional precision and consistency.
In contrast to CNC milling, where the cutting tool rotates and approaches the stationary workpiece from different angles, CNC turning revolves around rotating the workpiece in a chuck. This method is primarily employed for fabricating round or tubular shapes, allowing for the creation of more precise curved surfaces than would be feasible with CNC milling or other techniques.
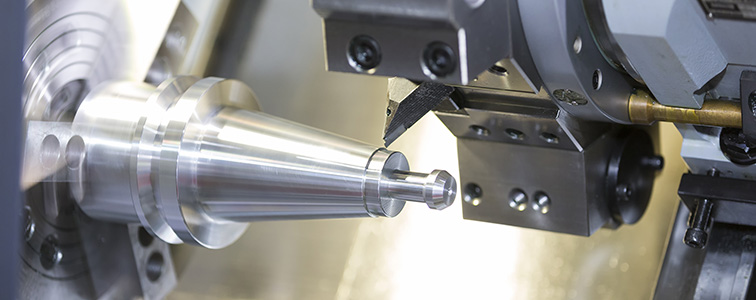

Applications of CNC Machining
• Manufacturing of complex parts:
CNC machining is widely used for the production of complex parts with tight tolerances and precise specifications. It can produce parts that are difficult or impossible to make with traditional manufacturing methods.
• Rapid prototyping:
CNC machining can be used to quickly produce prototypes for testing and validation. This allows engineers and designers to test their ideas and make adjustments before moving to mass production.
• Custom tooling and fixtures:
CNC machining can be used to create custom tooling and fixtures for specific manufacturing processes. This ensures that the manufacturing process is optimized for maximum efficiency and quality.
• Production of low-volume parts:
CNC machining can be used to produce low-volume parts economically. This is especially useful for niche products that require specialized parts or for replacement parts that are no longer produced.
• Aerospace and defense:
CNC machining is widely used in the aerospace and defense industries for the production of critical components that require high precision and accuracy.
• Medical device manufacturing:
CNC machining is used extensively in the production of medical devices such as implants and prosthetics. The high precision and accuracy of CNC machining ensure that these devices meet strict quality and safety standards.
• Automotive manufacturing:
CNC machining is used in the production of automotive parts, from engine components to body panels. It is especially useful for producing complex parts with high accuracy and precision.
Our Machining Capabilities
We have a comprehensive selection of CNC machines available at our facility, including over 25 machines, including twin spindle CNC turning/mill lathes, 5-axis mill/turns, and 4-axis vertical and horizontal machine centers. With our extensive range of precision CNC equipment, we are fully equipped to produce high standard parts with complex shapes and in various sizes.
• 3-axis CNC Machining
CNC machining operations typically involve milling along the X, Y, and Z axes, which allow the cutting tool to move in three directions: up and down, side to side, and back to front. 3-axis machining is a straightforward method that enables the cutting tool to move in these three directions.
• 4-axis CNC Machining
The 4-axis CNC machine produces parts using the same method as 3-axis machines, but it includes an additional A-axis that allows the cutting tool to rotate along the X-axis. This makes 4-axis CNC machining highly advantageous for cutting tasks that involve creating holes or cut-outs around a cylinder or inside an object.
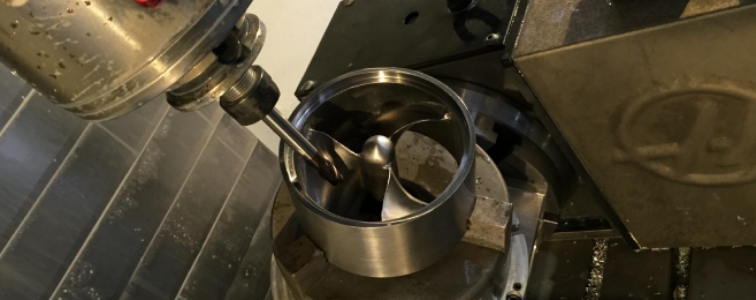
• 5-axis CNC Machining
5-Axis CNC machines include all the axes found in the 4-axis setup, supplemented by an additional B-axis. These machines are considered to be the most advanced CNC machines currently available in the market, and they are particularly well-suited for creating intricate parts and precise geometries, such as those required for artificial bones, aerospace components, and automotive applications. The 5th B-axis further enhances precision and control by rotating around the Y-axis in the X-Y-Z plane. Notably, 5-axis machines are also characterized by their speed and efficiency. They offer single-step machining, which significantly reduces lead time and enhances tool efficiency.
CNC Milling Machine Options
Unlike other parts creation processes like 3D printing, CNC milling machines subtract material from a block or sheet until the desired peace remains. This subtractive method is done using multiple types of cutting tools and surfaces that can rotate, revolve, tilt, and slide. Machines are frequently designated as horizontal, vertical, or multi-axis milling.
• Horizontal – The cutting tool moves in from one or both sides.
• Vertical – A tool presses against the mounted material much like a drill press.
• Multi-axis – Tools come from the top, sides, and on diagonal axes, as needed for more complex parts milling.
Besides the configuration of the cutting tools and materials, CNC milling operations also differ based on the type of cutting or material removal they do. These methods include surface, face, form, or angular milling.
• Surface – Material is cut away from the surface with a tool parallel to the part.
• Face – Material is removed using a perpendicular tool on one side.
• Form – Removing material in curves and contours using bespoke tools.
• Angular – Create grooves and joins using angled tools from different sides.
How the material gets held and the cutting or milling method both matter extensively when it comes to delivering the precise part created by the computer-aided design process. However, two other criteria go into a custom CNC milling job. These include how the material is mounted to the machine and held securely in place, and how the tools are changed during workpiece creation.
Of course, it is of the utmost importance that the material never shifts or vibrates excessively during the milling process. This would create discrepancies in the measurements of the plan and the final piece. CNC machines do not usually hold the material, and thus the finished part, on a spindle. They are instead held with a variety of vices and clamps or custom-made fixtures designed and created on one of these machines itself.
Some milling machines require manual tool changes between different parts of the milling procedure. One cutting tool does its job, the machine is stopped, a person changes to a new machine, and the work continues. Others use automatic tool changers that are set up ahead of time with all the necessary choices needed to complete a particular workpiece project. This is, of course, more convenient and hands-off.
Why Comely CNC?
• Streamlined process flow
At Comely CNC, our operations follow a dedicated process flow that minimizes risk, verifies raw materials, and ensures the production of high-quality prototypes and end parts consistently.
• Quick turnaround
Leverage our industrial-grade equipment to accelerate your product development cycles and hasten your time-to-market. With our expertise, we can help you overcome bottlenecks and fast-track your product development right away.
• Scalable and consistent manufacturing
Our additive manufacturing solutions prioritize scalability and repeatability, providing you with the flexibility to prototype or manufacture according to your budget without compromising print quality.
• Comprehensive finishing services
In addition to our precision printing capabilities, we also offer finishing solutions to enhance the aesthetic appeal of your parts. Our in-house finishing services are subject to the same stringent quality control measures for a lasting guarantee of quality.
• Quality and Consistency
We prioritize quality throughout the production process, ensuring consistent, high-quality end-use products.
• Cost and Profitability
Our competitive pricing adds value to client's businesses by delivering parts at a lower cost-per-part, making us one of the most competitive manufacturing businesses in China.
• One-Stop Shop
Our one-stop-shop approach streamlines the product development cycle, providing comprehensive services from design to finishing solutions that enhance the appearance and functionality of the final product.