Item No
|
SS6882 Cloun Beige
|
Description
|
Artificial Quartz
|
Color
|
beige,
|
Slab Size
|
3000x1400mm,3000x1600mm, 3200x1400mm, 3200x1600mm etc.
|
Thickness
|
12mm, 15mm, 18mm, 20mm, 30mm
|
Harness
|
7
|
Temperature Resistance
|
≥300ºC
|
Density
|
2.3~2.5g/cm3
|
Package
|
Packed directly in wooden crates, with safe support to protect the
surface & edges, and prevent rain and dust.
|
Payment terms
|
Usally T/T (30% deposit / 70% before loading ), 100% L/C at sight.
|
Service
|
Welcome Specified Size and Colors
|
Ideal Use:
|
Kitchen Countertops, bathroom vanity top, wall tile, wall cladding, floor tile,etc.
|
Engineered quartz countertops are made up
of 93% quartz and 7% resin and colour pigment. High per cent of quartz makes
the product very durable and hard. The colors of quartz countertops may be
variegated with flecks or swirls of various colors that give your countertops
the natural appearance of stone. These resins make the countertop more
resistant to household chemicals and cleaners than granite or marble. The
polymers also give quartz counters a non-porous surface that is 99.9% bacteria
free.
Quartz is non-porous. Unlike granite,
marble and concrete, quartz countertops don’t stain when put in touch with oil,
coffee, wine, tomato juice and similar liquids that are common in the kitchen.
Non-porous also means more hygienic as the surface doesn’t attract or retain
bacteria. Quartz is also quite durable, although the edges can chip, and it is
not quite as heat-resistant as granite. However, you can round the edges to
avoid chipping, and your quartz countertop should be fully resistant to normal
kitchen wear and tear.
The Production Process:
1.
The process begins with a strict inspection of raw materials.
2.
The natural quartz raw material and polymer resins and inorganic pigments are
put into the mixers and mix together.
3.
After mixing, pour them into a mold and form them into slab size.
4.
Pressing: Then the slab is compacted by a special vacuum and vibration process
at pressure machine.
5.
Then the slab is moved to the curing kiln and heated for a period time to make
their final strenth and srurdiness.
6.
Cut edges, flat , thicknessing and polishing surface to perfect finished.
7.
Finally, through quality inspection and plastic film packaging
Sample Room:
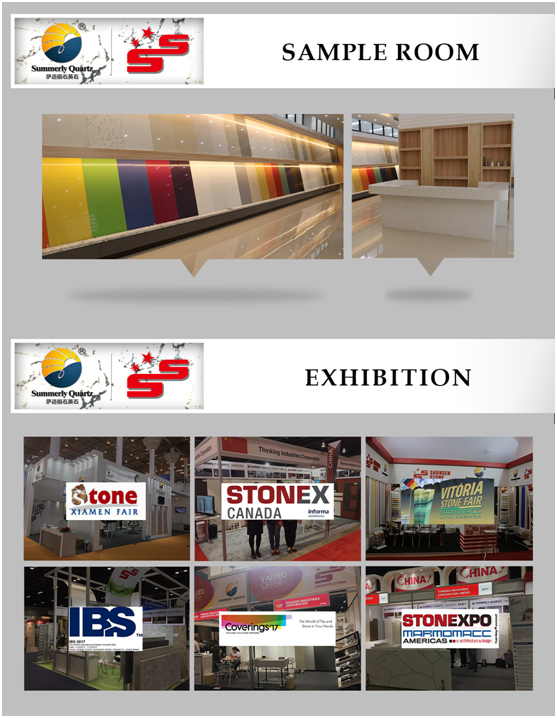