AGUS 32
AUTOMOTIVE GRADE UREA SOLUTION 32.5%
AdBlue Production Unit
TECHNICAL DESCRIPTION– BLUEBASIC EBR550L
The Bluebasic EBR550 plant is a containerized solution designed to produce AdBlue® according to ISO 22241, meeting with the highest standards of quality and according to VDA requirements with a maximum production capacity of 5500 L/Day.
The EBR550 production plant consists of four independent units:
1. Demineralization unit.
2. AdBlue® production unit.
3. Screw feeding unit.
4. Filling machine for bottles.
1. Demineralization unit
The plant is conceived to deliver 250L/h (5000L/day) of permeate stream with an electrical resistivity ≥10 MΩ.cm, starting from 0.8 m3/h of raw water with a maximum concentration of ions of about 800 mg/l (TDS) and conductivity is less than 1500µS/cm. This choice allows to cover most of the civil/industrial applications where it is expected to draw water from the local network (2 bars at least) by ensuring the production of high quality demineralized water (low conductivity) for industrial uses and, in particular, for the production of high purity AdBlue®.
During this phase, the feed water passes through double stages of reverse osmosis under pressure. As result, water is split into two streams: the permeate (demineralized water) and concentrate (a concentrated solution of impurities).
The key functions and components of this stage are:
· Pre-filtration of the feed water through disposable filters, which are carbon filter, sands filter and resin filter.
· Dosage of antiscalant and dechlorinating product.
· Filtration through osmotic membranes and ion exchange or EDI(Electrodeionization in short, optional).
· Reading/control of in-line conductivity.
· Permeate and concentrate streams management (delivery/recirculation).
· Flushing management.
The key functions and components of this stage are:
· Loading the bag(s) of urea through the screw feeder or by workers. If using screw feeder, every time loading urea 300KG around. If charging urea by workers, every time loading urea 32KG around.
· Transferring water using the pump from the demineralized storage tank to the stainless steel mixing tank. The demineralized water could be heated in the stoarge tank. Heating the water until it reaches a defined temperature. The heating system is optional.
· The weight of urea and the demineralized water are measured by the weigh scales installed under the mixing tank.
· Starting the production of AdBlue® by combining the demineralized water with the urea.
· Simulate a vortex inside the mixing tank in order to create the proper conditions to load the urea. The pump is used to create the vortex.
· After completion of this stage and in accordance with the quality requirements (measured by the weigh scales) of the final product, the system will be ready to transfer the AdBlue® to the outside storage tank. The pump is used to make this transferring through the double stages of filtrations.
· The entire system (demineralization and AdBlue® production stages) is handled by a Programmable Logic Controller (PLC) which manages among other things:
- The opening and closing of the pneumatic actuators valves, protection door.
- Flow of permeate and concentrate streams based on electrical conductivity.
- Quality of the product in accordance with the measurement of the weigh scales, the precision is 0.3%.
- The PLC can be connected to the Internet, and all condition of the machine could be checked remotely by the Bluebasic’s engineers.
- Materials: SS304
- Volume of the hopper: 300Kg urea;
- Three motors:
- Rotary Motor, 220V, 1.5Kw;
- Crusher Motor: 220V, 25W;
- Vibrator: 220V, 100W;
- Feeding speed: 1000Kg urea/Hour;
- Specification of the hopper: 1050×1050×1170cm;
- Floor space: 2200×1050×1500cm
The scope of this phase is to filling AdBlue® into 5L, 10L 20L bottles by manual workor. The filling machine contains an IBC tank on a weight scales, a circulation pump, a spray nozzle. The filling machine is also connected to the main machine, which condition can be monitored by PLC. In this phase, the compressed air is needed to control the spray nozzle.
The pressure of the compressed air: 4-6 bar.
Capacity: 1000L per hour.
Power: 370W.
Video Online view :
https://youtu.be/XvWPAq3j6JM
Brief introduction of flow sheet inside of machine:
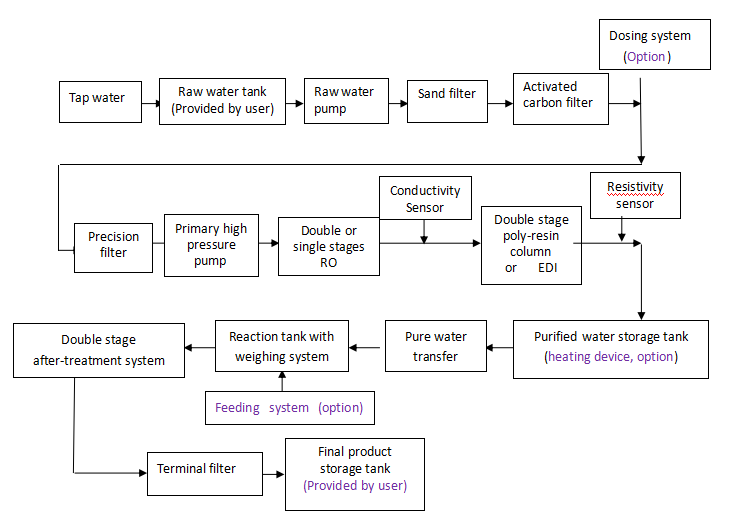
Total specification :
Model
|
EBR-550B
|
Size
|
1100(L)x1100(W)x1500(H)mm
|
Batch volume
|
100KG solution
|
Duration of every batch production
|
10minutes
|
Capacity(25℃)
|
600KG(550L)/hour
|
Material
|
304SS、FRB、PP、PVC
|
Gross weight
|
400KG
|
Gross power
|
3500W
|
power consumption per 1000KG AdBlue
|
6.4KW
|
Power of heating system(option)
|
8KW
|
Power of all pumps
|
High pressure pumps, 2x1kW
Mixing pump, 0.75kW
Pure water supplement pump, 0.55kW
Raw water pump, 0.55kW
|
Water treatment system
|
Double stages of Reverse Osmosis;
Ion exchange or EDI(Electrodeionization in short)
|
Voltage of power supply
|
220V-240V
|
Specification of the filters and spare parts
|
5x5.0µ(20inch)PPfilter,
5x0.22µ(10inch)filter,
exchange resin columns
|
certification
|
ISO9001-2015, VDA, VDA sublicense
|
Water supply requirements
|
0.8T/H, 0.2MPa, tap water is preferred
|
Demine water control
|
Resistivity no less than 12MΩ.cm
|
Waste water discharge
|
0.4T/Hour
|
Precision
|
0.3%
|
Touch screen
|
PLC programmed, remote control
|
Installation requirements
|
flat and stable ground, no dust on site
4 wheels at bottom of unit, portable
|
Shelf life
|
8-10 years at least
|
Optional
|
automatic feeding device;
Heating device (8KW electrical heating)
|
Device appearance and details as followed :
Outlook of main machine Key instrument displays
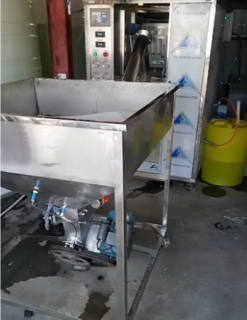
Feeding opening Screw feeder charging urea
Filling machine for 20L barrals :
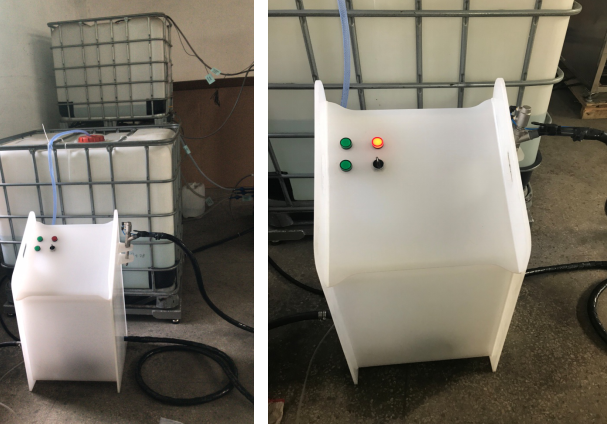
Automatic screw feeder:
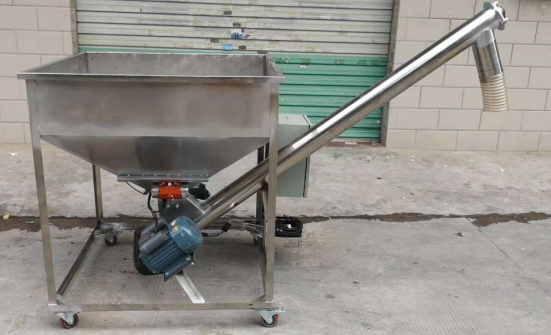
Remote operation interface schematic :
Login interface
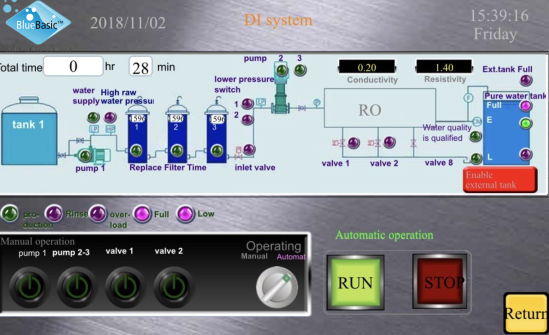
Demineralization unit
AdBlue production interface
Screw feeding interface
Filling machine controlling interface
Compared with traditional equipment
Intelligent AdBlue® machine:
1. It covers a minimum of 2.0 square meters
2. Intelligent touch screen, one button start unattended.
3. Full automatic control, single worker handled
4. Program setting and operation for quality assurance
5. Alarm function for replacement of supplies, equipment failure and unqualified water quality
6. Display of single batch output, cumulative output and concentration.
Traditional equipment:
- Large area occupied
- Manual operation and complex process
- Many people operate so that the error rate is large
- Human subjective control can easily affect product quality.
Production cost:
1. The first group filters, 7.0USD/30mt AdBlue® production.
2. The second group filters, 40USD/50mt AdBlue® production.
3. The polyresin exchange column, 480USD/ 100mt AdBlue®.
Total cost is 6.0USD per1000KG AdBlue®