Manganese steel casting have these properties:
Cafu's custom manganese steel casting contain mainly 1.1-1.3% carbon, 11.5-23% Mn and 1.7-2.3% Cr.
Furthermore, we offer customised products to meet our customers' specific requirements.
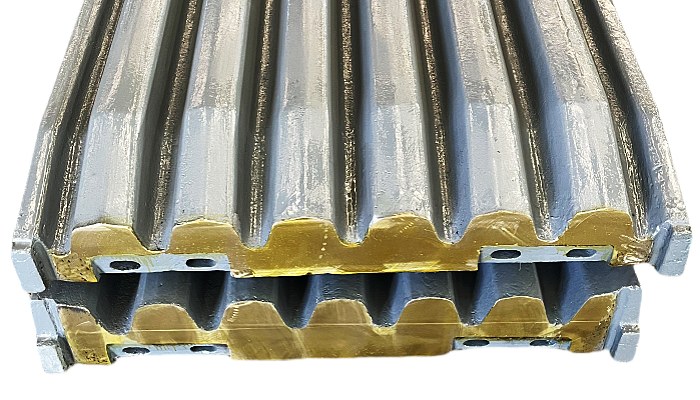
A number of manganese steel casting foundry have consistently sought to develop chemical element formulations for manganese steel castings that can be used in a variety of working conditions. Our high manganese steel casting, which are available in three main grades, have been well received by users from the outset.
Mat. |
Carbon% |
Mn% |
Cr% |
Si% |
Impact Toughness |
HB |
Mn13Cr2 |
1.15-1.3 |
11.5-14 |
1.7-2.3 |
0.3-0.8 |
≥147 J/cm2 |
HB≤300 |
Mn18Cr2 |
1.15-1.3 |
16.5-19 |
1.8-2.3 |
0.3-0.8 |
≥147 J/cm2 |
HB≤300 |
Mn22Cr2 |
1.1-1.45 |
20.5-23 |
1.8-2.3 |
0.3-0.8 |
≥147 J/cm2 |
HB≤300 |
Manganese steel casting are subjected to different heat treatment processes to obtain different material properties. This cast steel has high toughness and ductility, and the hardness of the castings can be selected according to different applications. As the hardness of the material increases, its wear resistance increases significantly, but correspondingly reduces the toughness of the material.
How heat treatment affects manganese steel casting?
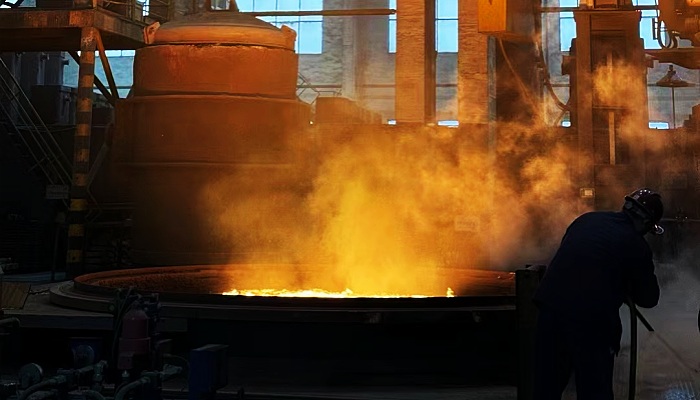
• Water toughening treatment:
This method enhances the toughness and wear resistance of manganese steel castings.
• Normalizing treatment:
Normalizing treatment can enhance the strength and hardness of manganese steel castings.
• Quenching treatment:
Quenching treatment can enhance the hardness and wear resistance of manganese steel castings, although it may result in a reduction in toughness.
The choice of heat treatment method will depend on the specific requirements of the manganese steel casting in question. Our aim is to select the most suitable process for your application, ensuring the best possible product performance.
Manganese casting is used in many applications.
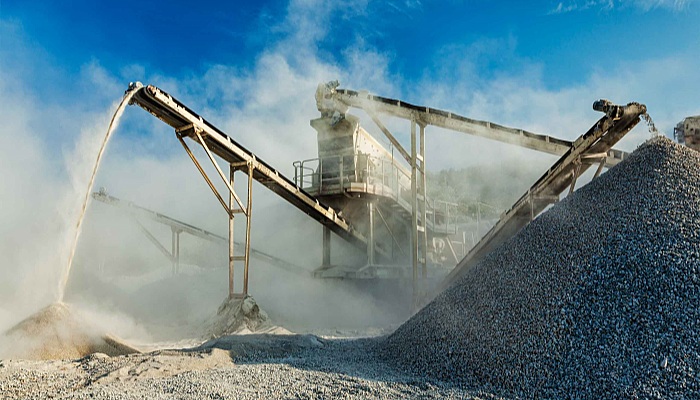
• Mining Industry:
Jaw plate of crusher, molar wall and crushing wall of cone crusher, etc., are used for crushing ores and withstand strong impact and abrasion.
•Mining apron feeder spare parts:
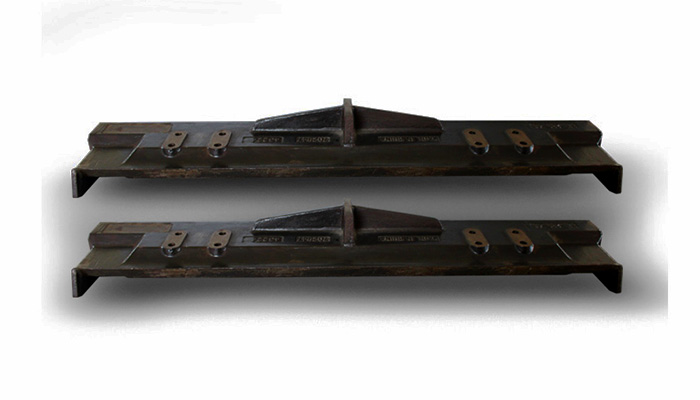
• Construction industry:
Concrete mixer blades and liners, which undergo friction from gravel during the mixing process.
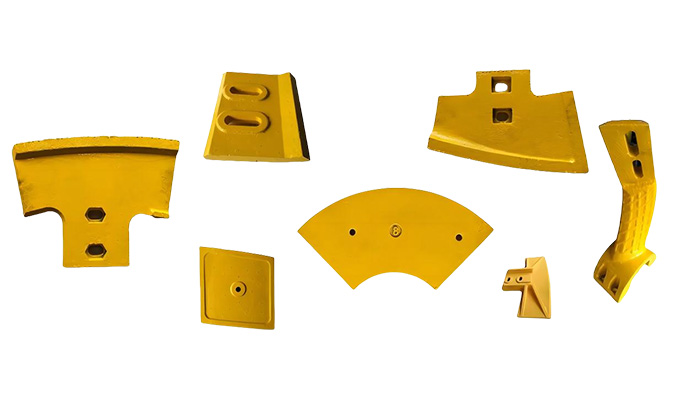
• Railway industry:
Components of railway turnouts, which need to withstand the enormous pressure and abrasion of passing trains.
• Cement Industry:
Liners and partitions of cement mills, which resist wear and tear when grinding materials.
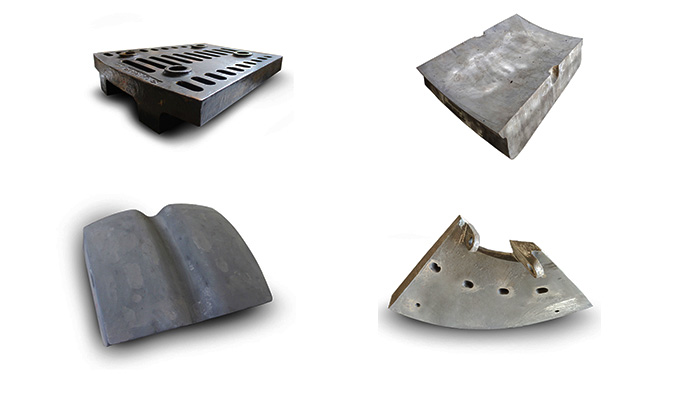
• Machinery Manufacturing Industry:
Bucket teeth, track plates, etc. of excavation equipment to cope with wear and impact during digging and movement.
Major facilities & quality control at manganese steel casting foundry:
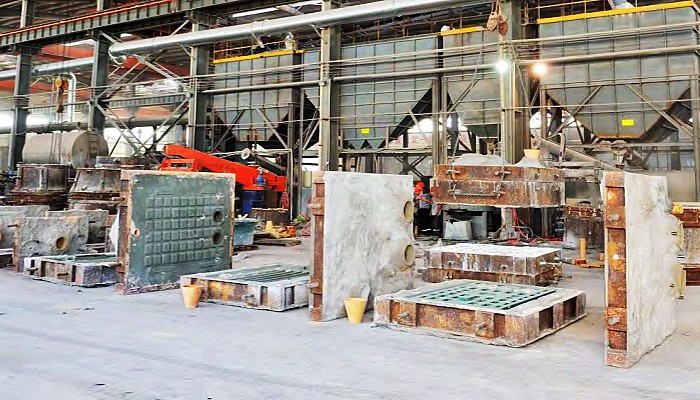
• Simulate pouring system.
• A large database of drawings and product mould to shorten the R&D cycle.
• 3D modelling.
• Advanced casting processes: sand-water-glass casting & vanishing-mould casting.
• Shot blast machine, medium frequency electric furnace, sand treatment equipment and moulding line, precision casting production line, environmental heat treatment furnace.
• Lean testing technology: raw material analysis room & mechanical property analysis room.
• Six rigorous tests: dimensional inspection, spectral composition analysis, colour probe (PT) test, hardness analysis, metallographic analysis, etc.
Cafu is one of your ideal choices when it comes to custom made manganese steel casting.
We are well versed in manganese castings for a variety of applications and have a comprehensive understanding of material properties. For different applications of high manganese steel castings, we use different quality control methods to strictly control the main production processes to ensure the best performance of casting quality.