Product Type:
|
Artificial Quartz Stone
|
Item No:
|
SQ6161
Arabescato White
|
Colors:
|
White
|
Composition:
|
More than 93% natural quartz, and nearly 7% resin and mineral pigment.
|
Size
|
93% quartz+7% resin and color pigments and others.
|
Thickness:
|
12mm , 15mm , 18mm , 20mm , 30mm,etc.
|
Surface
|
Polished or Honed or Customized.
|
Quality Control
|
Confirm Every Details Before Make the Rough Production
Thickness tolerance: ±0.5mm, ±1mm, 90 degree up polished
All products were checked by experienced QC before packed
|
Package
|
Strong seaworthy wooden crated with fumigation.
Inner packing: with foamed plastic materials packed inside.
Packed directly in wooden crates, with safe support to protect the
surface & edges, and prevent rain and dust.
|
Payment Term
|
T/T, 30% as deposit, 70% paid in 10 days after shipping date against the
copy of B/L.
|
Quartz is a man-made. Therefore, it won’t
chip or crack easily. Engineered stone surfaces do not require polishing to
keep them shiny and smooth, but they should be cleaned gently to maintain their
distinctive shine. You can will get a
more uniform color from engineered stone. The benefit in this is that
engineered stone used in the kitchen will perfectly match the design throughout
your home. This means you can add subtle color changes in the design such as
the curtains, the tile, etc.
Quartz countertops are one of the most
stain resistant products you can buy. Under normal use, stains are rare .For
stubborn stains and spills, a rounded
plastic knife should be used to remove dried foods or liquids on a quartz
surface. Dried paint or grease can be gently scraped away with a plastic knife.
Avoid using metal knives and utensils directly on the countertop, as metal may
scratch the quartz.
Ideal
Use:
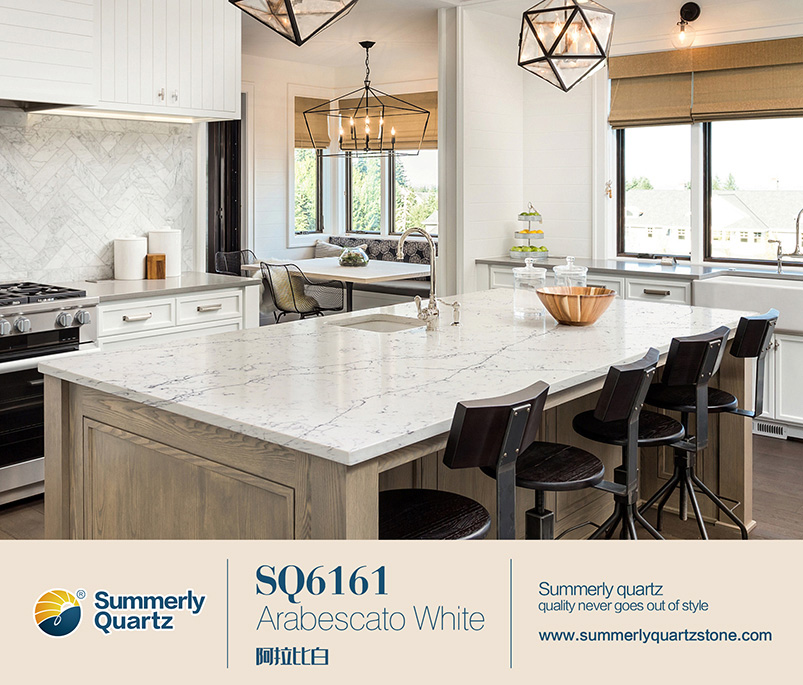
The Production Process:
1.
The process begins with a strict inspection of raw materials.
2.
The natural quartz raw material and polymer resins and inorganic pigments are
put into the mixers and mix together.
3.
After mixing, pour them into a mold and form them into slab size.
4.
Pressing: Then the slab is compacted by a special vacuum and vibration process
at pressure machine.
5.
Then the slab is moved to the curing kiln and heated for a period time to make
their final strenth and srurdiness.
6.
Cut edges, flat , thicknessing and polishing surface to perfect finished.
7.
Finally, through quality inspection and plastic film packaging
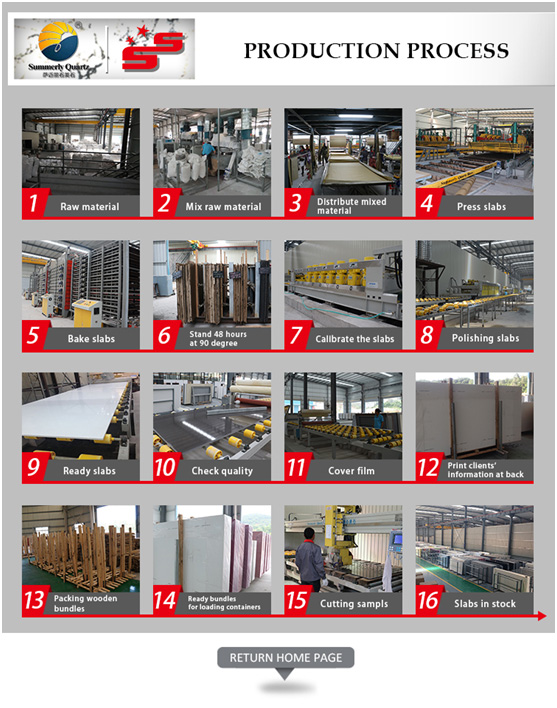