Item No
|
SS3820 Chaka Grey
|
Materials:
|
High purity acid-washed 93% quartz stone, 7% polymer
material and a small amount of inorganic pigment
|
Size:
|
Slabs size: 3000x1400mm,3000x1600mm, 3200x1400mm, 3200x1600mm etc.
Countertop: 48*26". 70*26", 78*26", 96"x26", 108"x26"
Vanity top:
22"x25", 22"x31",
22"x37", 22"x49", 22"x61", 22"x73"
Island:
72"x36", 96"x36",
96"x40",
108"x44"
|
Thickness:
|
12mm, 15mm, 18mm, 20mm, 30mm
|
Surface Finish:
|
Polished, Honed,etc.
|
Ideal Use:
|
Countertops, desk,
vanity top, bench top, island tops, bar tops, etc.
|
Quality Control
|
Thickness tolerance for tile: +-0.5mm;+-1mm.
All products are checked by experienced QC then packed.
|
Payment Terms
|
T/T, L/C at sight
|
Packing:
|
Fumigated Wooden Bundle, Wooden Crate
|
Quartz
slabs are made using natural quartz, at about 93%, which are bonded together
with a non-porous resin,pigments. Quartz countertops are the most durable
countertop material that you can find. Besides the hardness and non-porous
attributes on the quartz stone, it can be cut into beautiful countertops.
Quartz is also very consistent in appearance and pattern.
Quartz
is a non-porous material, which makes it extremely durable. This means that
there are reduce the likelihood that
bacteria will grow on the surface of the countertop. They require less maintenance when compared
to natural stone countertops.
Polished
surfaces have a great appearance and are easy to keep clean and maintain. Avoid
using rough surface cleaners such as a steel wool sponge; use a non-abrasive
sponge to clean your kitchen countertops. All you need to use is soap, warm water, and a wash cloth .
The Production Process:
1.
The process begins with a strict inspection of raw materials.
2.
The natural quartz raw material and polymer resins and inorganic pigments are
put into the mixers and mix together.
3.
After mixing, pour them into a mold and form them into slab size.
4.
Pressing: Then the slab is compacted by a special vacuum and vibration process
at pressure machine.
5.
Then the slab is moved to the curing kiln and heated for a period time to make
their final strenth and srurdiness.
6.
Cut edges, flat , thicknessing and polishing surface to perfect finished.
7.
Finally, through quality inspection and plastic film packaging
Laboratory:
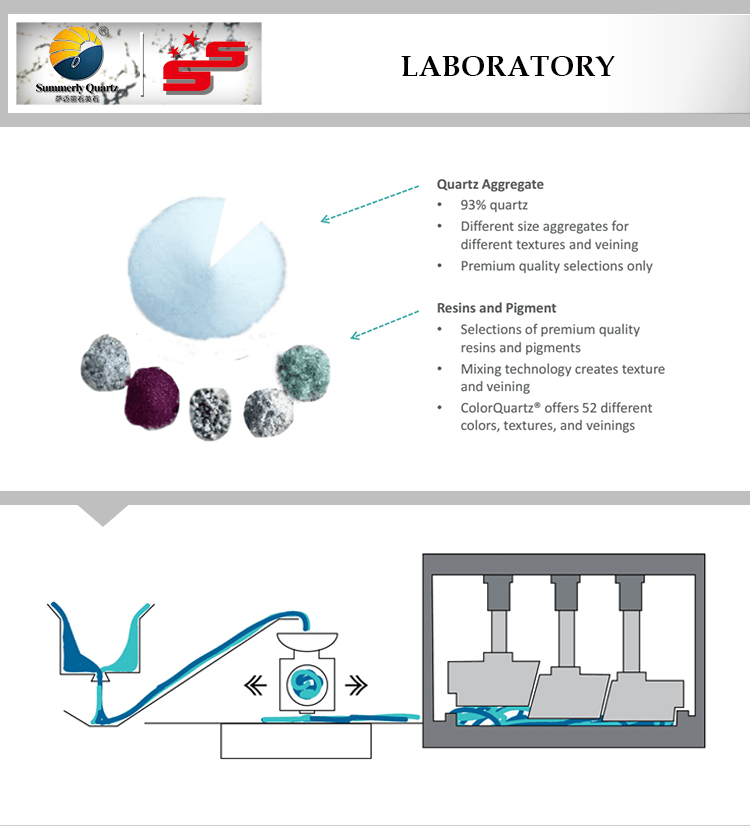