Imported CUN66A1G 365nm UV LEDs SVC 10W UV Lights is for paper currency fluorescent detection and jewelry fluorescent detection. CUN66A1G UV Lights is used quartz glass lens, aluminum nitride holder. Its optical power is 1800mW and its irradiation angle is 115 deg.
Description of SVC 10W UV Curing Lights installing UV Flashlight :
1.High power UV LED series are designed for high current operation and high power output applications.
2.It is incorporates state of the art SMD design.
3.Z5 NUV LED is ideal UV light source for curing, printing, and detecting applications.
Features and Benefits of CUN66A1G 365nm Ultraviolet Light Emitting Diodes :
1.High power output
2.Designed for high current operation
3.SMT type
4.Lead free product
5.RoHS compliant
Key Applications of High Efficiency CUN66A1G UV LED Lights for Curing :
UV Curing, printing, coating, adhesive, counterfeit detection / security, UV torch, fluorescence photography, dental curing, crime inspection, oil leak detection
Performance Characteristics of Stable 365nm UV LED Curing Lights :
Electro - optical characteristic at 1A (Ta=25℃, RH=30%)
Parameter
|
Symbol
|
Value
|
Unit
|
Peak wavelength
|
λp
|
367
|
Mm
|
Radiant Flux
|
Φe
|
1800
|
mW
|
Forward Voltage
|
VF
|
3.7
|
V
|
Spectrum Half Width
|
Δ λ
|
9
|
nm
|
View Angle
|
2Θ1/2
|
120
|
deg.
|
Absolute Maximum Rating
Parameter
|
Symbol
|
Value
|
Unit
|
Min.
|
Typ.
|
Max.
|
Forward Current
|
IF
|
-
|
-
|
1400
|
mA
|
Junction Temperature
|
Tj
|
-
|
-
|
90
|
ºC
|
Operating Temperature
|
Topr
|
- 10
|
-
|
85
|
ºC
|
Storage Temperature
|
Tstg
|
- 40
|
-
|
100
|
ºC
|
Thermal resistance (J to S)
|
RθJ-s
|
-
|
5.8
|
-
|
ºC/W
|
Notes :
1.Peak Wavelength Measurement tolerance : ±3nm
2.Radiant Flux Measurement tolerance : ± 10%
3.Φe is the Total Radiant Flux as measured with an integrated sphere.
4.Forward Voltage Measurement tolerance : ±3%
5.RθJ-S is the thermal resistance between chip junction to solder.
The PCB is made of aluminium and the size of PCB is 2.5cm by 2.5cm
Characteristics Graph of Korea CUN66A1G UV Flashlight Light without Ozone :
Fig 1. Spectrum, Ta=25℃, IF=1A
Fig 2. Forward Voltage vs. Forward Current, Ta=25℃
Mechanical Dimensions of UV Z5 High Power CUN66A1G UV LED :
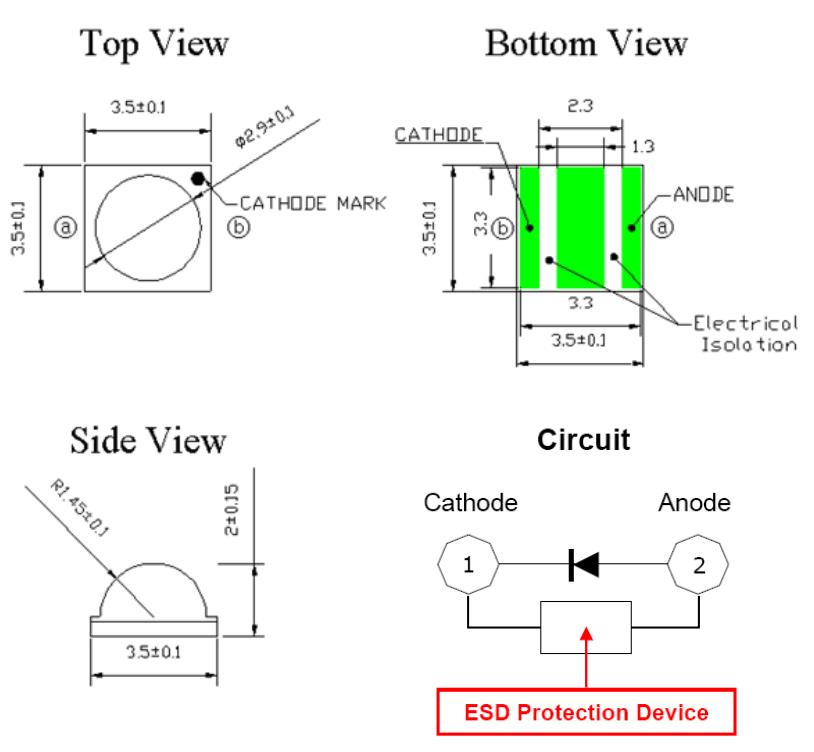
1.All dimensions are in millimeters.
2.Scale : none
3.Undefined tolerance is ± 0.2mm
Recommended Solder Pad of Quartz Glass Lens Seoul 365nm UV LED Lights CU66A1G :
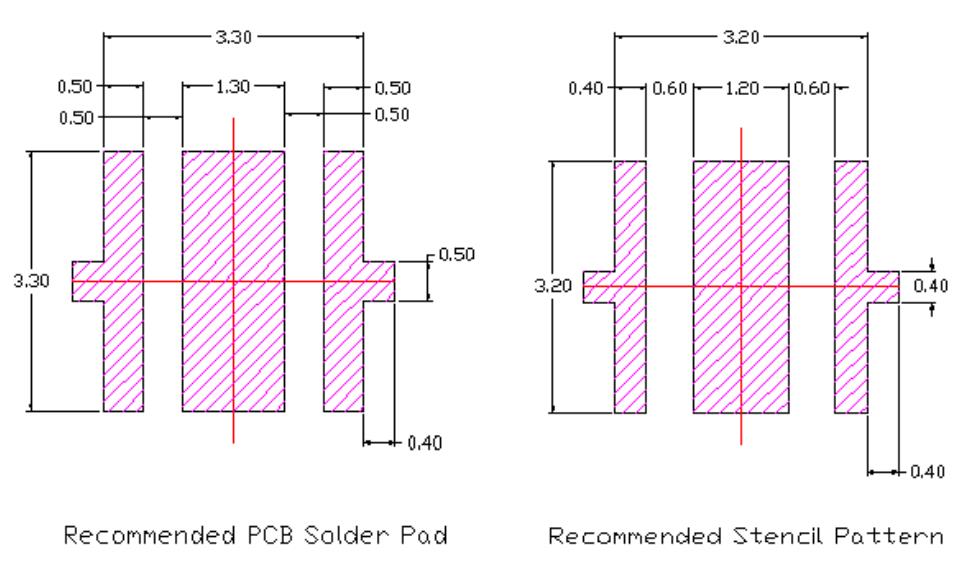
1.All dimensions are in millimeters.
2.Scale : none
3.This drawing without tolerance is for reference only.
Handling of Silicone Resin for Imported Seoul UV LEDs Soldering on PCB :
1.During processing, mechanical stress on the surface should be minimized as much as possible. Sharp objects of all types should not be used pierce the sealing compound.
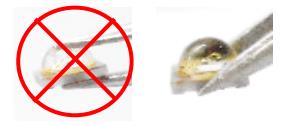
2.In general, LEDs should only be handled from the side. By the way, this also applies to LEDs without a silicone sealant, since the surface can also become scratched.
3.When populating boards in SMT production, there are basically no restrictions regarding the form of the pick and place nozzle, except that mechanical pressure on the surface of resin must be prevented. This is assured by choosing a pick and place nozzle which is larger than the LED’s reflector are.
4.Silicone differs from materials conventionally used for the manufacturing of LEDs. These conditions must be considered during the handling of such devices. Compared to standard encapsulants, silicone is generally softer, and the surface is more likely to attract dust. As mentioned previously, the increased sensitivity to dust requires special care during processing. In cases where a minimal level of dirt and dust particles cannot be guaranteed, a suitable cleaning solution must be applied to the surface after the soldering of components.
5.SVC suggests using isopropyl alcohol for cleaning. In case other solvents are used, it must be assured that these solvents do not dissolve the package or resin. Ultrasonic cleaning is not product with acid or sulfur material in sealed space.
6.Please do not mold this product into another resin (epoxy, urethane, etc) and do not handle product with acid or sulfur material in sealed space.
7.Avoid leaving fingerprints on silicone resin parts.
8.Silicone lens are sticky. During the SMT process, LED may adhere to cover or can be rotated. So SMT conditions must be adjusted. Please slow down the feeding speed. It can reduce the sticking problem.
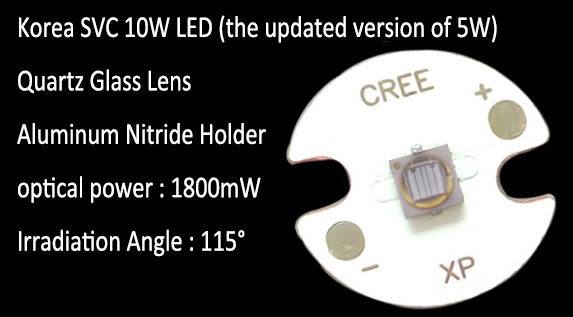