Advantages of ABIS Aluminum PCBs
-
Low Cost
-
Environmentally Friendly
-
Heat Dissipation
-
Higher Durability
-
Lightweight
Aluminum PCBs Introduction
-Definition
Aluminum base is a CCL, a type of base material of PCBs. Aluminum core board is a composite material composed of copper foil, a dielectric layer, an aluminum base layer and aluminum base membrane with a good heat dissipation. Using a very thin layer of thermally conductive but electrically insulating dielectric, which is laminated between the metal base and the copper layer. The metal base is designed to draw heat away from the circuit through the thin dielectric.
-Application
aluminum pcb assembly's widely used for the modifier and sparker on fire for motorcycle and mobile, power LED, sound box, power supply module and acoustics shielding system etc.
ABIS Metal Core PCB Manufacturing Capacity
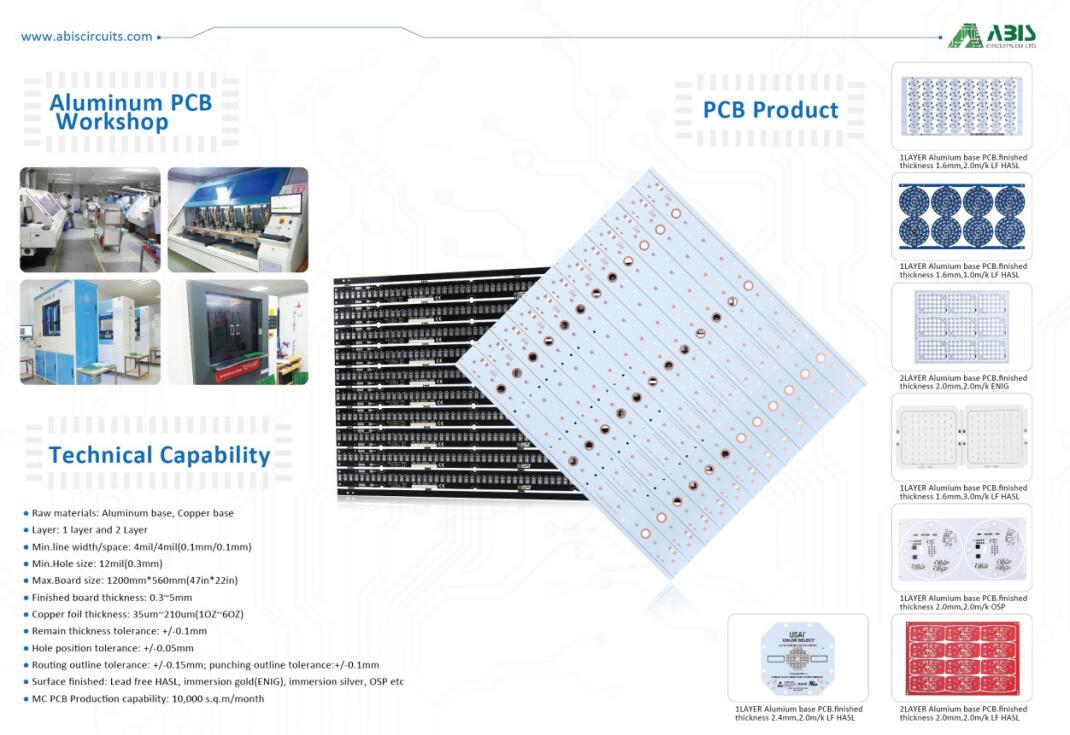
Item
|
Speci.
|
Layers
|
1~2
|
Common Finish Board Thickness
|
0.3-5mm
|
Material
|
Aluminum Base, Copper base
|
Max Panel Size
|
1200mm*560mm(47in*22in)
|
Min Hole Size
|
12mil(0.3mm)
|
Min Line Width/Space
|
3mil(0.075mm)
|
Copper Foil Thickness
|
35μm-210μm(1oz-6oz)
|
Common Copper Thickness
|
18μm, 35μm, 70μm, 105μm.
|
Remain Thickness Tolerance
|
+/-0.1mm
|
Routing Outline Tolerance
|
+/-0.15mm
|
Punching Outline Tolerance
|
+/-0.1mm
|
Solder Mask Type
|
LPI(liquid photo image)
|
Mini. Solder Mask Clearance
|
0.05mm
|
Plug Hole Diameter
|
0.25mm--0.60mm
|
Impedance Control Tolerance
|
+/-10%
|
Surface finish
|
Lead free HASL, immersion gold(ENIG), immersion sliver, OSP, etc
|
Solder Mask
|
Custom
|
Silkscreen
|
Custom
|
MC PCB Production Capacity
|
10,000 s.q.m/monthly
|
ABIS Aluminum PCBs Lead Time
As the current mainstream, we mostly do single aluminum PCB, while it is more difficult to do double sided aluminum PCB.
Small Batch Volume
≤1 sq meter
|
Working Days
|
Mass Production
>1 sq meter
|
Working Days
|
Single Sided
|
3-4 Days
|
Single Sided
|
2-4 weeks
|
Double Sided
|
6-7 Days
|
Double Sided
|
2.5-5 weeks
|
Technical Parameter
NO
|
Test item
|
Technology request
|
Unit
|
Test Result
|
1
|
Peel Strength
|
A
|
≥ 1.0
|
N/mm
|
1.05
|
After thermal stress (260 ordm;C )
|
≥ 1.0
|
N/mm
|
1.05
|
2
|
Blister test After Thermal stress (288 ordm; C, 2min)
|
288ordm; C 2 min
No delaminating
|
/
|
OK
|
3
|
Themal Resistance
|
≤ 2.0
|
ordm; C /W
|
0.65
|
4
|
Flammability(A)
|
FV-O
|
/
|
FV-O
|
5
|
Surface Resistivity
|
A
|
≥ 1 × 10 5
|
M Ω
|
5.0 × 10 7
|
Constant humidity treatment
(90%,3 5 ordm;C ,96h)
|
≥ 1 × 10 5
|
M Ω
|
4.5 × 10 6
|
6
|
Volume Resistivity
|
A
|
≥ 1 × 10 6
|
M Ω· m
|
1.0 × 10 8
|
Constant humidity treatment
(90%, 35 ordm; C ,96h)
|
≥ 1 × 10 6
|
M Ω· m
|
1.9 × 10 7
|
7
|
Dielectric Breakdown (DC )
|
≥ 25
|
Kv/mm
|
31
|
8
|
Dielectric constant (1MHz)
(40 ordm;C, 93% , 96h)
|
≤ 4.4
|
/
|
4.2
|
9
|
Dielectric dissipation factor (1MHz )
(40ordm; C ,93%,96h)
|
≤ 0.03
|
/
|
0.029
|
10
|
Accelerated aging experiment
(125 ordm; C ,2000h)
|
/
|
The laminate base should no wrinkles,no crack,no delaminating or no pine
|
/
|
OK
|
11
|
High low temperature impact test
(-50 ordm; C , 15min, 80ordm; C , 15min TOTAL DO 15 ~ 20 Circulation)
|
Peel Strength
|
/
|
N/mm
|
1.39 ~ 1.64
|
Surface Resistivity
|
/
|
M Ω
|
1.9 × 10 8 ~6.4 × 10 8
|
How ABIS Working Out Manufacturing Difficulties of Aluminum PCB?
-
Raw materials are strictly controlled: The pass rate of incoming material above 99.9%. The number of mass rejection rates is below 0.01%.
-
Copper Etching Controlled: the copper foil used in Aluminum PCBs is comparatively thicker. If the copper foil is over 3oz however, the etching requires width compensation. With the high precision equipment imported from Germany, the min width/space we can control reaches 0.01mm. The trace width compensation will be designed accurately to avoid the trace width out of tolerance after etching.
-
High Quality Solder Mask Printing: As we all know, there is a difficulty in solder mask printing of aluminum PCB due to copper thick. This is because if the trace copper is too thick, then the image etched will have a large difference between trace surface and base board and solder mask printing will be difficult. We insist on the highest standards of solder mask oil in the whole process, from the one to the two-time solder mask printing.
-
Mechanical Manufacturing: To avoid reducing electrical strength caused by the mechanical manufacturing process, involves mechanical drilling, molding and v-scoring etc. Therefore, for low-volume manufacturing of products, we prioritize using the electric milling and professional milling cutter. Also, we pay high attention to adjusting the drilling parameters and preventing burr from generating.
Packaging & Delivery
ABIS CIRCUITS Company is not only trying to give customers a good product, but also pay attention to offering a complete and safe package. Also, we prepare some personalized services for all the orders.
-Common packaging:
-
PCB: Sealed bag, Anti-static bags, Suitable carton.
-
PCBA: Antistatic foam bags, Anti-static bags, Suitable carton.
-
Customized Packaging: The carton outside will be printed the name of the customer address, mark, the customer needs to specify the destination and other information.
-Delivery Tips:
-
For small package, we advise to choose by Express or DDU service is the quickest way.
-
For heavy package, the best solution is by sea transportation.
Business Terms
-Accepted Delivery Terms
FOB, CIF, EXW, FCA, CPT, DDP, DDU, Express Delivery, DAF
--Accepted Payment Currency
USD, EUR, CNY.
-Accepted Payment Type
T/T, PayPal, Western Union.
Quotation from ABIS
To ensure an accurate quote, be sure to include the following information for your project:
-
Complete GERBER files: including the BOM list
-
Quantities: Choose Num (pcs)
-
Dimensions: Height X Width mm
-
Turn time: working days
-
Panelization Requirements
-
Materials Requirements
-
Finish requirements
Your custom quote will be delivered in just 2-24 hours, depending on the design complexity.
Please keep us informed for any interests!
ABIS cares every your order even 1 piece!