LKQ Thermal Mass Gas Flow meter
LKQ series thermal type gas mass flowmeter is a mass flow measurement and monitoring meter,which can detect air, natural gas, hydrogen, oxygen, chlorine, nitrogen and ammonia, ammonia, coal gas, phosgene, flue gas and various chemical mixtures, without pressure and temperature compensation. It can be widely used in petroleum, chemical, metallurgy, electric power, water treatment, paper, food, medicine, cement, textile and various production, scientific research units for process control and gas flow measurement.
Features
■ Direct measurement of mass flow of gas without pressure and temperature compensation;
■High repeatability, high reliability, high stability and high precision;
■Range range width: up to 1000:1 or more;
■Explosion-proof, anti-corrosion design, suitable for harsh conditions, corrosive occasions;
■High sensitivity, especially suitable for flow measurement of large diameter and low flow rate;
■Eextremely small pressure loss and almost negligible;
■Diverse structure, flexible installation, convenient loading and unloading, easy to use, basically maintenance;
■ LCD display, clear and intuitive, showing both instantaneous flow and cumulative flow, so that you can see more clearly and more directly.
Product Classification Table 1
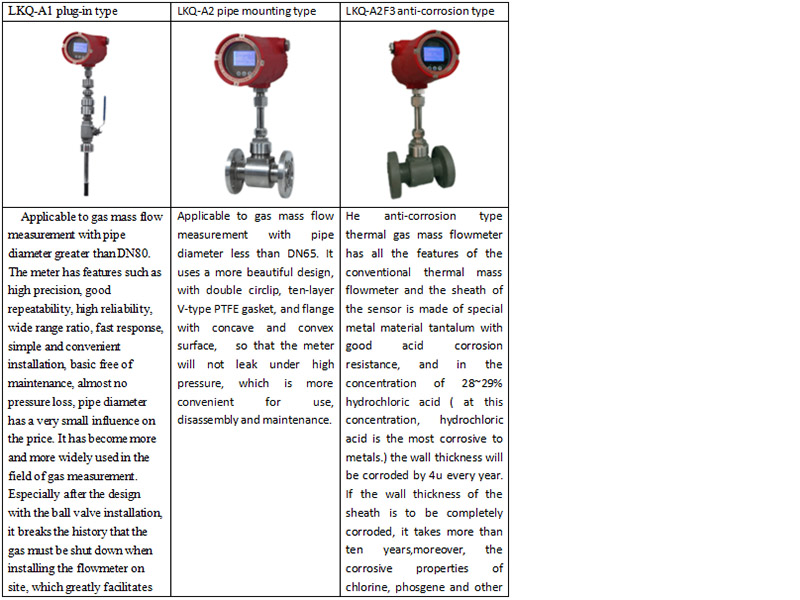
Instrument selection Table 2
LKQ |
-□ |
□ |
□ |
□ |
□ |
□ |
□ |
Code description |
Installation form |
|
|
|
A1 |
|
|
|
Plug-in type |
|
|
|
A2 |
|
|
|
Pipe mounting type |
|
Power supply |
|
|
|
B1 |
|
|
|
220VAC |
|
|
|
B2 |
|
|
|
24VDC |
|
Output signal |
|
|
|
C1 |
|
|
|
4~20mA |
|
|
|
C2 |
|
|
|
RS485 |
|
|
|
|
C3 |
|
|
|
HART |
|
Whether the meter has a display |
|
|
|
D1 |
|
|
|
No display at the meter head |
|
|
|
D2 |
|
|
|
Header instantaneous flow display |
|
|
|
|
D3 |
|
|
|
Header instantaneous and cumulative flow display |
|
Whether it has intelligent flow totalizer |
|
|
|
E1 |
|
|
|
No flow totalizer |
|
|
|
E2 |
|
|
|
With intelligent flow totalizer |
|
Special requirements |
|
|
|
F1 |
|
|
|
No special requirements |
|
|
|
F2 |
|
|
|
Flameproof |
|
|
|
|
F3 |
|
|
|
Corrosion resistant (sensor is tantalum material) |
|
|
|
|
F4 |
|
|
|
High temperature type (150-250℃) |
|
Flowmeter and pipe seal connection |
|
|
|
L1 |
|
|
|
Continuous flow assembly and disassembly device (ball valve) <0.8Mpa |
|
|
|
L2 |
|
|
|
Continuous flow assembly and disassembly device (ball valve) + high pressure seal assembly <2.0Mpa |
|
|
|
|
L3 |
|
|
|
Simple threaded assembly <0.8Mpa |
|
|
|
|
L4 |
|
|
|
Threaded component + high pressure seal assembly <2.0Mpa |
|
|
|
|
W1 |
|
|
|
Flange type components >2.0Mpa |
|
|
|
|
W2 |
|
|
|
Flange type heat dissipation component (high temperature type) |
|
|
|
|
W3 |
|
|
|
The sampling pipe is flanged to the pipe under test on site |
|
|
|
|
W4 |
|
|
|
The sampling pipe is threaded to the pipe under test on site |
|
Practical pipe diameter |
|
|
|
|
|
|
|
Based on the actual inner diameter of the pipe at the user site (for example, the inner diameter of the pipe is 300mm, it is indicated by the number 300) |
Product structure size and installation
1、Structure size Table 3
Nominal diameter |
Overall dimension |
Flange dimension |
|||
DN(mm) |
L(mm) |
H(mm) |
D(mm) |
D1(mm) |
D2(mm) |
25 |
125 |
320 |
115 |
85 |
65 |
40 |
135 |
345 |
150 |
110 |
84 |
50 |
140 |
358 |
165 |
125 |
99 |
80 |
194 |
390 |
200 |
160 |
132 |
100 |
230 |
410 |
220 |
180 |
156 |
2、Installation requirements
a. The length of the straight pipe section of the pipe to be tested at the installation of the flowmeter shall meet: upstream 20D distance, downstream 10D distance (D is the inner diameter of the pipe). By using our rectifying flowmeter (pipe diameter ≤ DN100), the length requirements of the front and rear straight pipe sections can be greatly reduced.
b. The flow regulating valve should be installed as least 10D far from downstream of the flowmeter . If it must be installed at the front end, it should be far away from the measuring point.