Item No:
|
SS6013
Marmara White
|
Color:
|
White
|
Size:
|
Slabs size: 3000x1400mm,
3000x1600mm, 3200x1600mm,etc
Countertop: 48*26".
70*26", 78*26", 96"x26", 108"x26"
Vanity top:
22"x25", 22"x31", 22"x37", 22"x49",
22"x61", 22"x73"
Island: 72"x36",
96"x36", 96"x40", 108"x44"
|
Thickness:
|
12mm, 15mm, 18mm, 20mm, 30mm
|
Bulk Density:
|
>2.30g/cm3
|
Mohs′ Hardness:
|
5~7
|
Surface Finish:
|
Polished.Honed
|
Application:
|
Countertops,
vanity top, worktops, table tops, bench top, island tops, backsplashes,
shower stalls, tub surrounds,etc.
|
Quality control:
|
Color
difference control,Safe packing,
Thickness
tolerance: /-1mm
All
products are checked by experienced QC piece by piece and then pack
|
Payment Terms:
|
30%
T/T as deposit +70% T/T before loading container
|
Quartz has been one of the most popular
materials for kitchen and bathroom surfaces for many years. The versatility of
this stone is what makes it a preferable option. It comes in an amazing variety
of colors and patterns. But no matter what your choice, once installed
correctly, you will have a rich and luxurious space for your absolute
relaxation.
Quartz is made of 93% natural quartz and 7%
resins. The resins act as a sealant and are the reason why you will never have
to seal your quartz slabs.Engineered stone used to fabricate countertops is
acid-resistant and non-absorptive. This makes it stain resistant and hygienic –
perfect for kitchen countertops where spills are common and bacteria could
accumulate if those spills were absorbed into the countertop. An ordinary daily
wipe-down with warm water and mild soap is all that is needed to maintain a
quartz countertop.
Quartz is scratch and chip resistant to
everyday use. This means you can be
worry free for years to come.Because of this natural advantage, quartz
countertops are also heat, and bacteria
resistant ,corrosion resistance, making them the perfect surface for kitchens
and bathrooms,dinning room,etc.
The Production Process:
1.
The process begins with a strict inspection of raw materials.
2.
The natural quartz raw material and polymer resins and inorganic pigments are
put into the mixers and mix together.
3.
After mixing, pour them into a mold and form them into slab size.
4.
Pressing: Then the slab is compacted by a special vacuum and vibration process
at pressure machine.
5.
Then the slab is moved to the curing kiln and heated for a period time to make
their final strenth and srurdiness.
6.
Cut edges, flat , thicknessing and polishing surface to perfect finished.
7.
Finally, through quality inspection and plastic film packaging.
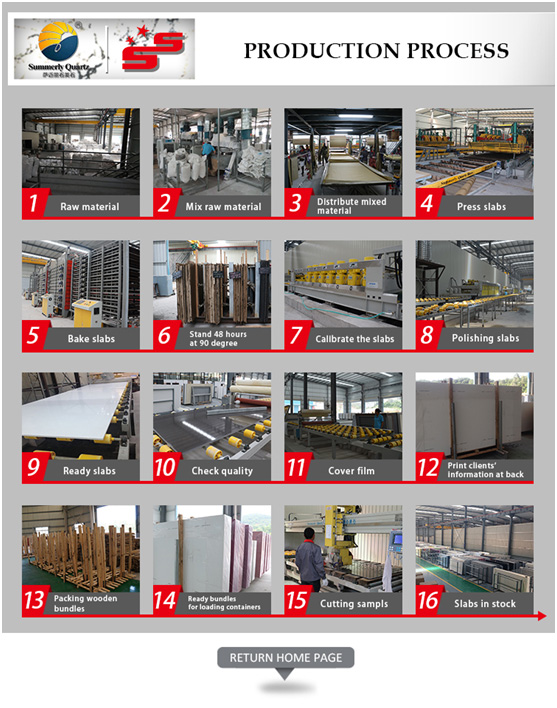
Laboratory:
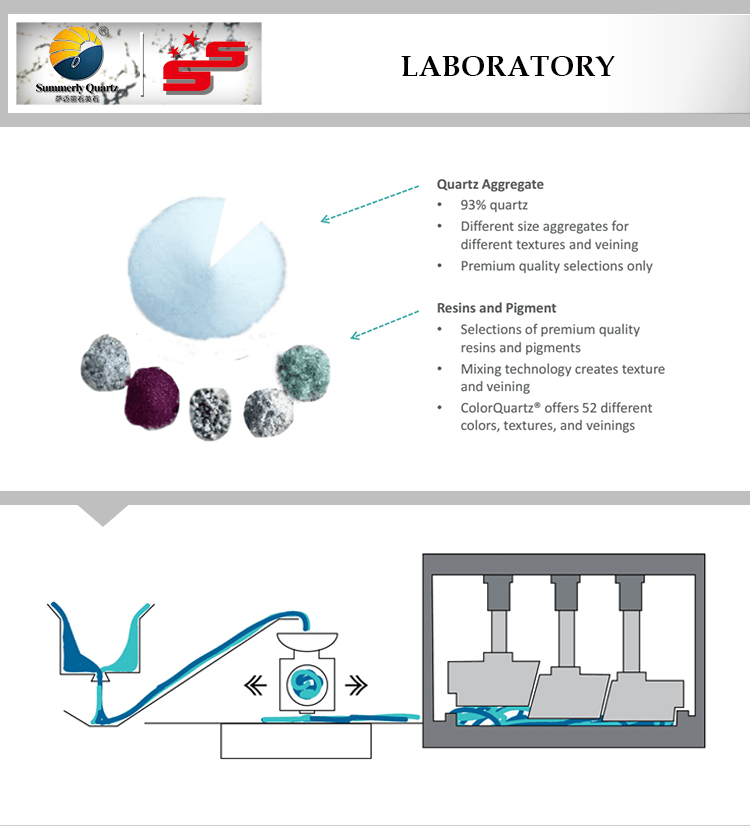