Product Description
PDCPD-RIM is a paste resin composed of DCPD as the main raw material, supplemented by polymer rubber, antioxidant, main and auxiliary catalysts, and time regulator.
All added substances comply with international ROSH norms. It is generally composed of A and B two-component.
Content |
A Liquid |
B Liquid |
Appearance |
Transparent/light yellow viscous liquid |
Black Viscous Liquid |
Viscosity (30℃) |
200-380cps |
200-380cps |
A+B=1:1 In-Molding Mixing |
Initial tackifying time (Mold temperature 25℃) |
5-30S |
Suitable injection time (Mold temperature 70℃) |
≤23S |
Curing time (Mold temperature70℃) |
150±30S |
Molding shrinkage of parts (thickness ≥4mm) |
10% |
Warranty Period |
0-40℃,Nitrogen seal intact,≥6 months |
PDCPD Properties VS Other Materials'
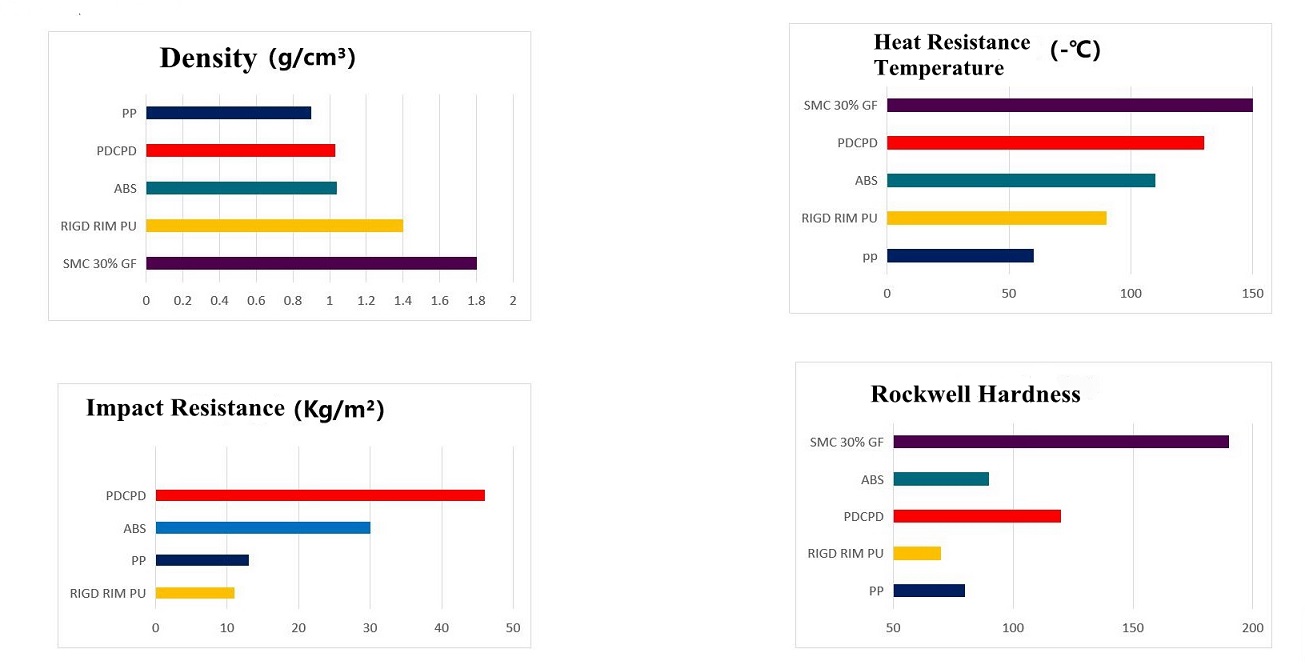
PDCPD Industry Application
PDCPD is most suitable for the manufacture of construction machinery, agricultural machinery, trucks, automobile coverings, integrated large-scale molding products represented by sanitary equipment, and purification tanks. It is the ideal material to replace glass fiber reinforced plastic, some plastics, metal sheet metal parts, carbon fiber, and alloy in the future, and it is also the high-quality choice for lightweight equipment in many new industries such as new energy automobile, wind power generation, unmanned aerial vehicle, tunnel template, robot and so on, and the application field is extremely broad, and it can be widely used in the fields of automobile manufacturing, construction engineering template, agricultural machinery, military, civil, medical, scientific research and national defense.
Especally, PDCPD materials are used in the production of automotive parts, replacing metal materials.
PDCPD Products Properties Test Reference
Content
|
Unit
|
Testing Method
|
Content
|
Unit
|
Testing Method
|
Tensile strength
|
47.5MPa
|
GB/T 1040.2-2006
|
Rockwell hardness
|
115
|
GB/T3398.2-2008
|
Tensile modulus
|
1900MPa
|
GB/T 1040.2-2006
|
Distortion temperature
|
110.5
|
GB/T1634.2-2004
|
Elongation at break
|
12.30%
|
GB/T 1040.2-2006
|
Density
|
1.03g/cm³
|
GB/T1033.1-2008
|
Compressive strength
|
60.8MPa
|
GB/T 1041-2008
|
Glass transition temperature
|
169℃
|
GB/T19466.2-2004
|
Bending strength
|
75.6MPa
|
GB/T9341-2008
|
Burning horizontally
|
HB40
|
GB/T2408-2008
|
Bending modulus of elasticity
|
2053MPa
|
GB/T9341-2008
|
Water Absorption
|
0.10%
|
GB/T1034-2008
|
Notched impact strength
of cantilever beam (23℃)
|
33.1
|
GB/T1843-2008
|
Automotive interior combustion
Performance (burning rate)
|
A-0
|
GB 8410-2006
|
Notched impact strength of
cantilever beam (-40℃)
|
12.8
|
GB/T1843-2008
|
Rockwell hardness
|
115
|
GB/T3398.2-2008
|
Outstanding Advantage of PDCPD materials
- High strength, light weight, easy molding, low energy consumption, no emissions, environmentally friendly materials.
- The best choice to replace fiberglass, metal carbon steel, stainless steel. It is the best choice for complex and large vehicle coverings
- Low energy consumption, only need to maintain a certain mold temperature, and the reaction itself exothermic. No need to use high-power heating equipment for a long time
- Less residual reaction, material in the mold reaction degree is high, fast, out of the mold almost no residual reaction, do not need to worry about deformation.
- The viscosity is low, liquid DCPD viscosity is very low, can be filled with complex shape molds in a short time, especially suitable for complex shape products.
- Simple surface treatment, good adhesion to paint, no need to clean when painting.
- Waste material can be recycled! Because it is pure hydrocarbons, there is no toxic emissions; it will be heated to 380 degrees high-temperature deodorizing enzymes into liquid, decomposed into new components, used as asphalt improver.