PP/PE Thermoforming Packaging Films in Medical Packaging
PP/PE film, also known as polypropylene/polyethylene film, is a type of flexible packaging material commonly used in various industries, including medical device packaging. It is a multil film that combines the properties of polypropylene (PP) and low density polyethylene (PE) to provide specific characteristics and performance.
PP is a thermoplastic polymer that offers excellent forming characteristics and dimensional stability. It can be easily thermoformed at temperatures ranging from 95°C to 115°C, allowing it to be shaped into different packaging configurations to accommodate the specific needs of medical devices like syringes, needles, feeding tubes, and in-vitro devices. PP also provides good puncture resistance, ensuring the protection of the packaged products.
PE, on the other hand, is known for its high transparency, moisture resistance, and low thermal sealing temperature. These properties make it an ideal material for creating a barrier to protect medical devices from moisture, oxygen, and other contaminants. Additionally, PE has good adhesive features, enabling it to be securely sealed to coated or uncoated medical-grade paper.
The combination of PP and PE in the PP/PE film brings together the desirable properties of both materials. The film exhibits excellent seal strength, ensuring the integrity of the package during transportation and storage. It also has low haze, which means it provides good visibility of the packaged products. The film's moisture resistance helps to maintain the quality and functionality of the medical devices throughout their shelf life.
Moreover, PP/PE film can be used on various types of form fill seal machines, making it compatible with different packaging processes. Its wide operating temperature range and sealing features contribute to a cost-effective packaging solution for medical device manufacturers.
PP/PE film is a versatile packaging material that offers thermoforming capabilities, puncture resistance, high transparency, good adhesive features, excellent seal strength, low haze, moisture resistance, and low thermal sealing temperature. These properties make it well-suited for packaging medical devices with the necessary protection, visibility, and functionality requirements.
Main Properties:
Good thermoforming
Forming temperature :95°c - 115°c
Puncture resistance
High transparency
Good bonding properties
Excellent sealing strength
Low fog
Excellent moisture resistance
Low heat sealing temperature
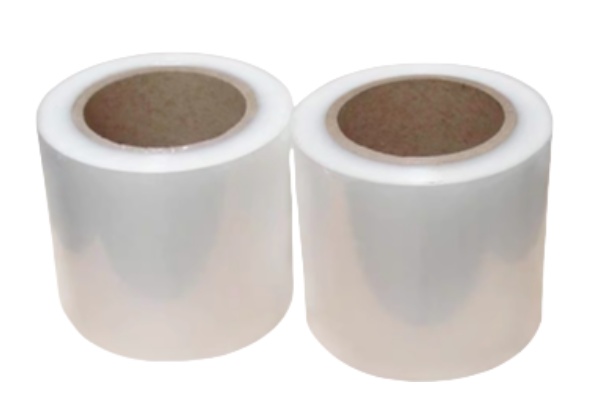
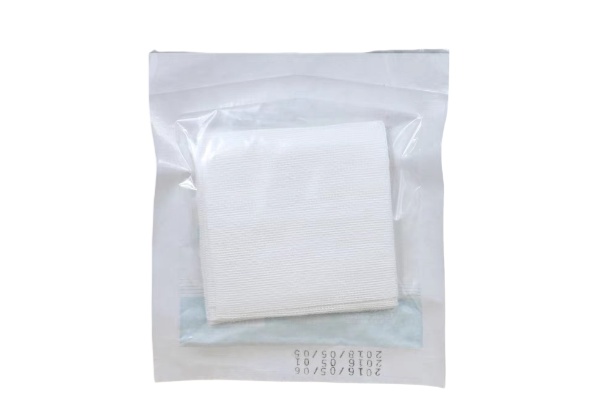
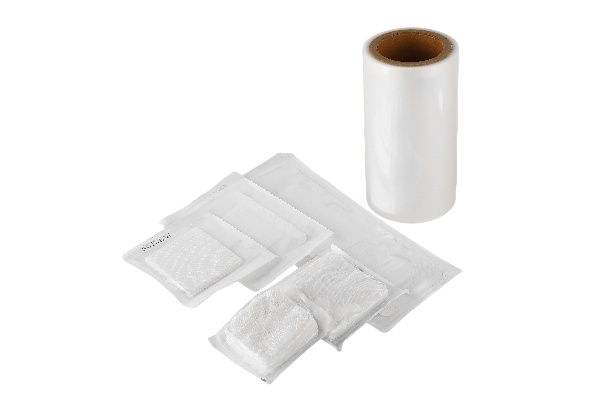