Feature:
-
Fully retain the advantages characteristics of QS6 series servo driver.
-
AC sine wave control, torque smoothly and without pulsation.
-
2500 ppr incremental photoelectric encoder, high positioning accuracy, rotary positioning accuracy up 1/10000R.
-
Speed ratio up to 1:5000, from low speed to high speed torque characteristics are stable.
-
High-speed arithmetic processing FPGA, maximum motor speed up to 5000RPM.
-
A rich complete set of parameters that can be configured to run different operating modes, so meet different demand.
-
Position, speed, torque control mode, using widely.
-
Adopt intelligent space vector control algorithm (SVPWM), could produce greater torque and less noise.
-
Up to three times the overload design, with a load capacity greater.
-
Perfect protection: over current, overvoltage, overheating and encoder failure, etc.
-
Perfect condition monitoring functions, such as the position error, motor speed, feedback pulse, command pulse and so on.
Specifications
1.QS7 has FPGA software platform with high-performance
2.application with the best wiring design
3.stable and convenient
QS7AA020M is a new generation of universal servo drive products based on QS optimization and improvement, adhering to the QS series of excellent quality, more stable and more convenient. The QS7AA020M servo controllers are more mature and stable with rich and complete data. New adding 485 communication function makes to connect with the upper computer software or controller more convenient and reliable.
Feature
-
The characteristics of last generation QS servo drivers have been fully retained.
-
AC sine wave control, smooth torque, no impulse.
-
2500 line incremental photoelectric encoder, high positional accuracy, rotation positional accuracy can reach 1/10000R.
-
Speed ration can be as large as 1:5000, has stable torque characteristics from low speed to high speed.
-
Adopting high speed FPGA processing, motor fastest rotation speed can be 5000RPM.
-
Rich and complete parameter setting can be configured with different ways of working and operating characteristics to adapt to different requirements.
-
Possess position, speed and torque control mode, has applications in a wide range.
-
Use intelligent Space Vector control (SVPWM), has much larger torque and much less noise than traditional SPWM.
-
Up to three times overload design, stronger load ability.
-
Perfect protection function: over current, overvoltage, over heat, encoder abnormal etc.
-
Perfect condition monitoring function, such as positional deviation, rotate speed, feedback impulse, command impulse etc.
QS7AA020M AC Servo Driver Paramenter:
Input Voltage
|
AC220V -15%~+10%
|
Driver Current
|
20A
|
Matching Motor
|
400W~750W motor
|
Using Temperature
|
Working environment temperature:45°C
Storage environment temperature:-40°C~55°C
|
Relative Humidity
|
40%~80% (none condensing)
|
Atmosphere
|
86-106kpa
|
Control Mode
|
Position control;JOG control;Speed control;Torque control ;Position and speed control;Inside pulse control;Electric tool carrier control
|
Pulse Command
|
Pulse+ Direction;CW + CCW Pulse;Two-phase AB orthogonal pulses
|
Control Precision
|
0.01%
|
Response Frequency
|
≤200Hz
|
Pulse Frequency
|
≤500kHz
|
Speed Ratio
|
1:5000
|
Regenerative Brake
|
Internally Installed
|
Electronic Gear
|
1/30000~30000/1
|
Overload Capacity
|
≤300%
|
Feedback Pulse
|
2500p/r, frequency division can be set arbitrary within 0-128
|
Display Function
|
Rotate speed, motor current, motor torque, current location,positional deviation, command impulse count, current pulse frequency, space rate, I/O diagnose, analog input values, etc
|
Protection Function
|
Over current, overvoltage, low voltage, overload, over heat, lack phase, over speed, ncoder abnormal, out of tolerance, mode abnormal alarm etc.
|
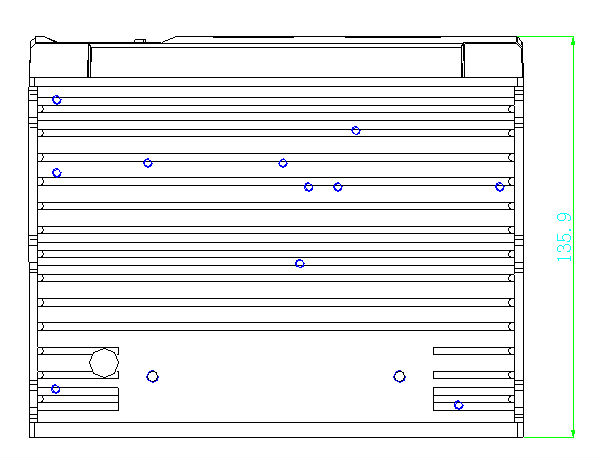

<img
Parameters:
Input Voltage
|
AC220V -15%~+10%
|
Driver Current
|
20A
|
Matching Motor
|
≤750W Low-inertia Motor
|
Using Temperature
|
Work:45℃ Storage:-40℃~55℃
|
Relative Humidity
|
40%~80% with no condensation
|
Atmosphere
|
86-106kpa
|
Control Mode
|
①Position control ②JOG control ③Speed control ④Torque control ⑤Position and speed control
⑥Inside pulse control ⑦Electric tool carrier control
|
Pulse Command
|
①Pulse+ Direction ②CW + CCW Pulse ③ Two-phase AB orthogonal pulses
|
Control Precision
|
0.01%
|
Response Frequency
|
≤200Hz
|
Pulse Frequency
|
≤500kHz
|
Speed Ratio
|
1:5000
|
Regenerative Brake
|
Internally Installed
|
Electronic Gear
|
1/30000~30000/1
|
Overload Capacity
|
≤300%
|
Feedback Pulse
|
2500p/r, Frequency division can be set arbitrary within 0-128
|
Display Function
|
Motor speed, motor current, motor torque, motor position, the position deviation,
the number of command pulses, the pulse frequency, the straight-line speed, input and output diagnostic
|
Protection Function
|
Over speed, over current, overvoltage, under voltage, overload, super bad,
encoder fault, the temperature is too high, the internal chip failure, module failure
|
QS7AA020M AC Servo Motor Drives matching 100-750W motor
QS7AA020M交流伺服电机驱动匹配100-750W马达