Product Name
|
SS2804-Pure-Green
|
Colour
|
Green
|
Material
|
93% pure quartz
crystal, with 7% of resins, color pigments and others .
|
Size
|
3000x1400mm,3000x1600mm,
3200x1400mm, 3200x1600mm etc.
|
Thickness
|
12mm;15mm;
18mm; 20mm; 30mm,etc
|
Abrasion Resistance
|
49
|
Specular Gloss
|
44.5
|
Impact Resistance
|
7.72 J
|
Application
|
Kitchen countertops,table
tops, island tops, bathroom vanity top, wall tile,etc.
|
Sample
|
Free Small Quartz
Sample
|
Packing
|
Packed with strong
wooden crates and foam, film inside
|
Quartz
is a material that has been gaining much attention in recent years. Composed of
natural quartz crystals, quartz countertops are one of the most beautiful and
durable countertop selections for your home. Amongst being a household
favorite, quartz countertops are loved for their heat- and stain-resistant
properties, making them one of the most durable countertops on the market.
Quartz countertops are scratch-, stain-, and heat-resistant, which provides the
chef with ease will cooking. While it is heat-resistant, extremely high
temperatures can burn the material, so be sure to use caution.
For day do day cleaning you can
use just soap, water and a soft cloth.Harsh chemicals that contain bleach or
ammonia can damage quartz. Those chemicals are usually found in other household
cleaners. Make sure to avoid those chemicals and simply use mild soap or
detergent instead. Quartz is perfect for being low maintenance as you will
never have to worry about any long term cost commitment. You will never have to
take into account any sealing or treatments every year, like you do with
natural stones.
The Production Process:
1. The process begins with a strict inspection of
raw materials.
2. The natural quartz raw material and polymer
resins and inorganic pigments are put into the mixers and mix together.
3. After mixing, pour them into a mold and form
them into slab size.
4. Pressing: Then the slab is compacted by a
special vacuum and vibration process at pressure machine.
5. Then the slab is moved to the curing kiln and
heated for a period time to make their final strenth and srurdiness.
6. Cut edges, flat , thicknessing and polishing
surface to perfect finished.
7. Finally, through quality inspection and
plastic film packaging.
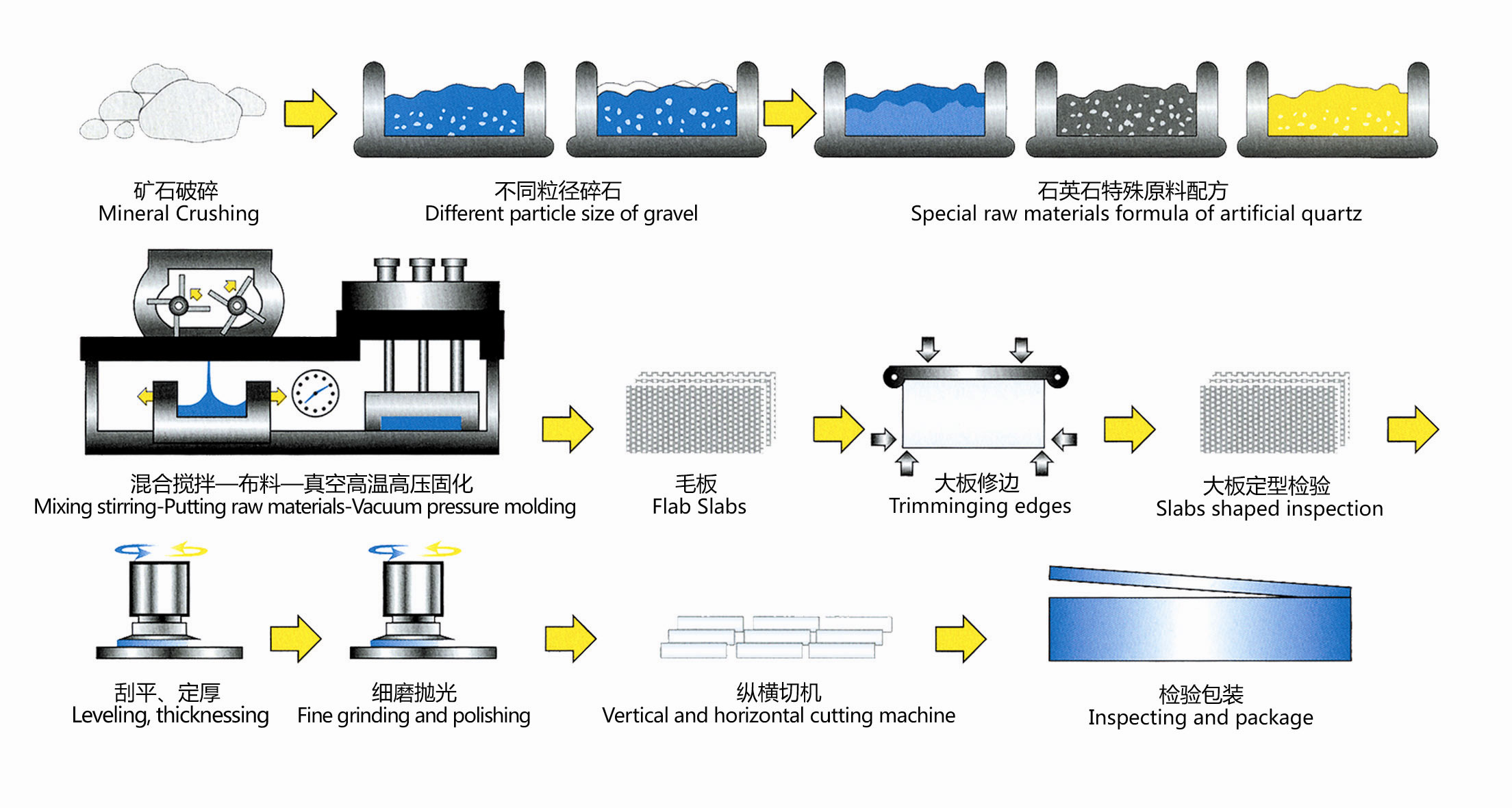