Model
No
|
SS3845 Maria
|
Composition
|
93
% pure quartz crystal, with 7 % of resins, color pigments and others .
|
Size
|
Slabs
size: 3000x1400mm,3000x1600mm, 3200x1400mm, 3200x1600mm etc.
Cut-to-size:
1200x600mm, 600x600mm,600x300mm,
600x400mm, 300x300mm,800x800mm;etc.
Counter
top: 48*26". 70*26", 78*26", 96"x 26", 108"x
26"
Island: 72"x 36", 96"x 36", 96"x 40",
108"x 44"
Vanity top: 22"x 25", 22"x 31", 22"x 37",
22"x 49", 22"x 61", 22"x 73"
|
Thickness
|
12
mm, 15 mm, 18 mm, 20 mm, 30 mm
|
Thickness
tolerance
|
±1mm
|
Harness
|
7
Mohs
|
Quality
Control
|
Polished
degree:90 degree or up.As customs' requirement
Thickness
tolerance: /-1mm
All
products checked by experienced QC and then pack
|
Service
|
We
can offer high quality, competitive price and swift delivery.
|
Samples
|
Free
Small Quartz Sample
|
Ideal
Use:
|
worktops, backsplashes, shower stalls, Furniture,etc.
|
Quartz countertops are many good qualities
such as their attractive appearance, durability and the fact they don’t have
some of the weaknesses of natural stone. Also called engineered stone
countertops, quartz countertops are here to stay. Here is a look at their
strengths.
• Quartz countertops are
available in many different colours.
• Quartz stone is a
non-porous material.therefore it does not require a sealing-ever.
• Durability as a result
of being made from one of the hardest minerals on earth.
• Available in a range of
colours and patterns.
• Quartz countertops are
resistant to scrapes . Furthermore, they are immune to stains as well as
microorganisms since they are not permeable.
The Production Process:
1.
The process begins with a strict inspection of raw materials.
2.
The natural quartz raw material and polymer resins and inorganic pigments are
put into the mixers and mix together.
3.
After mixing, pour them into a mold and form them into slab size.
4.
Pressing: Then the slab is compacted by a special vacuum and vibration process
at pressure machine.
5.
Then the slab is moved to the curing kiln and heated for a period time to make
their final strenth and srurdiness.
6.
Cut edges, flat , thicknessing and polishing surface to perfect finished.
7.
Finally, through quality inspection and plastic film packaging
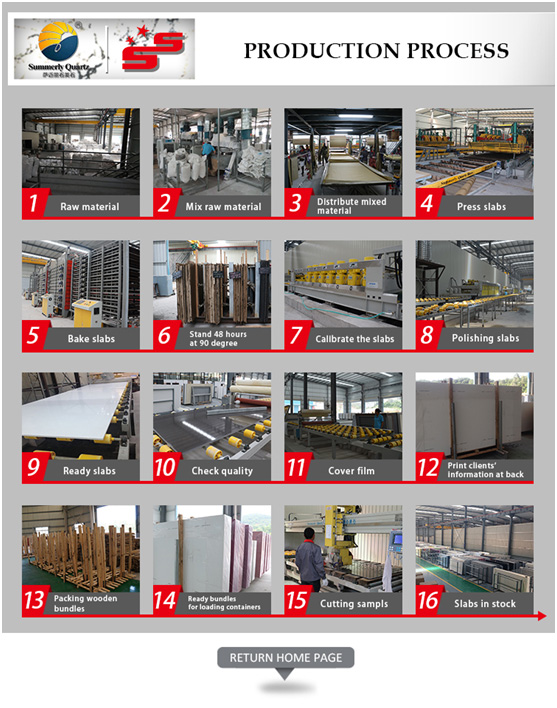
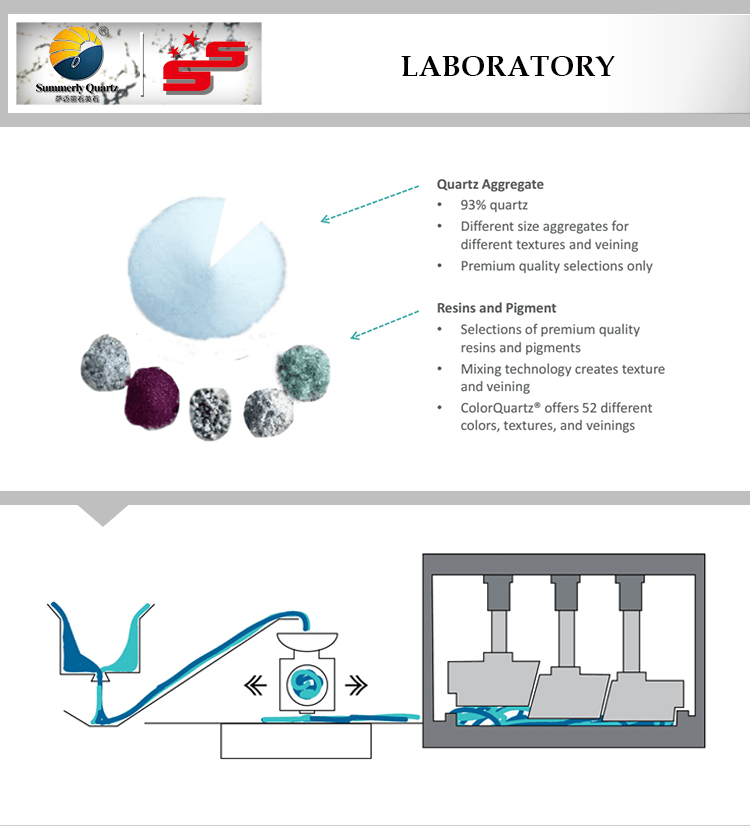