Product Name
|
SS-V007
Sofia
|
Slab Size
|
Slabs size:
3000x1400mm,3000x1600mm, 3200x1400mm, 3200x1600mm etc.
Cut-to-size: 1200x600mm, 600x600mm,600x300mm,
600x400mm, 300x300mm,800x800mm;etc.
Counter top: 48*26".
70*26", 78*26", 96"x 26", 108"x 26"
Island: 72"x
36", 96"x 36", 96"x 40", 108"x 44"
Vanity top: 22"x
25", 22"x 31", 22"x 37", 22"x 49",
22"x 61", 22"x 73"
|
Thickness
|
12mm,15mm,18mm,20mm,30mm,etc.
|
Surface Finish
|
Polished or Honed or
Customized
|
Water Absorption
|
<0.05%
|
MOQ
|
100 Square meters
|
Quality Control
|
Polished degree:90 degree
or up.As customs' requirement
Thickness tolerance:
/-1mm
All products checked by
experienced QC and then pack
|
Application
|
Countertop, worktop,
table top, Bar Top, Bathtub, Sink,etc.
|
Quartz countertops are manufactured with a
combination of hard quartz crystals and durable resin polymers that make them
extremely resilient. Low maintenance requirements make quartz countertops
appealing to many homeowners. All
designs are custom made since it is an engineered Quartz, so the selections are
diverse, and you are guaranteed to find the colors you are looking for.
Conversely, Granite and Marble you would have to choose from Nature’s menu. But selection is limited
compared to Quartz.
Quartz countertops have grown in popularity
as homeowners discovered what the earliest quartz pioneers knew - when the
natural mineral quartz is improved upon by man's ingenuity, quartz countertops
can compete with other natural stone countertops in every way. As a manmade
material, not only is quartz widely available, it can be easily manufactured
for unique sizing and unique shapes, including circles and curves.
Production Engineering:
1. The process begin with a rigorous
inspection of raw materials.
2. Feeding natural quartz raw material and
polymer resins and inorganic pigments in to mixers and blending them together.
3. After stirring the mixture, then pouring
them into a mold and form them into slab size.
4. Pressing: Then the slab is compacted by a
special vacuum and vibration process at pressure machine.
5. The slab then moved to the curing kiln and
heated for a period time which give them ultimate strength and solidity.
6. Trimming edges, leveling , thicknessing
and polishing surface to perfect finished.
7.Finally, the quartz stone slabs passed
through quality inspection and packed with a plastic film.
Packing wooden
crate (slab) wooden box (tiles/
countertop)
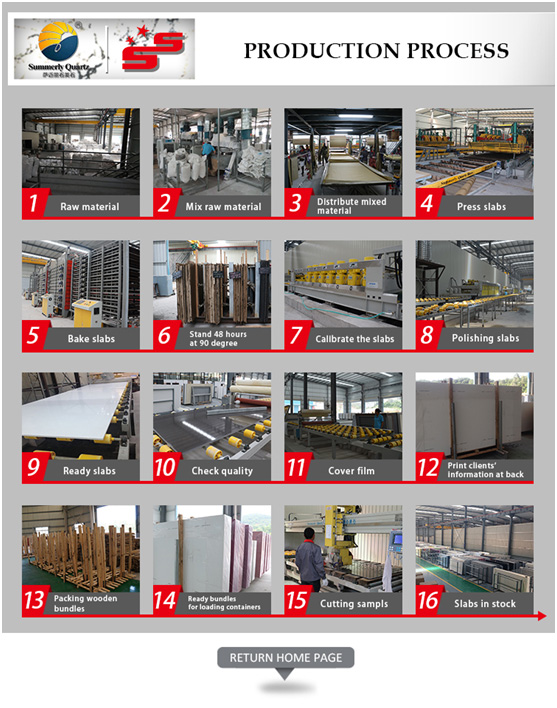
Lboratory:
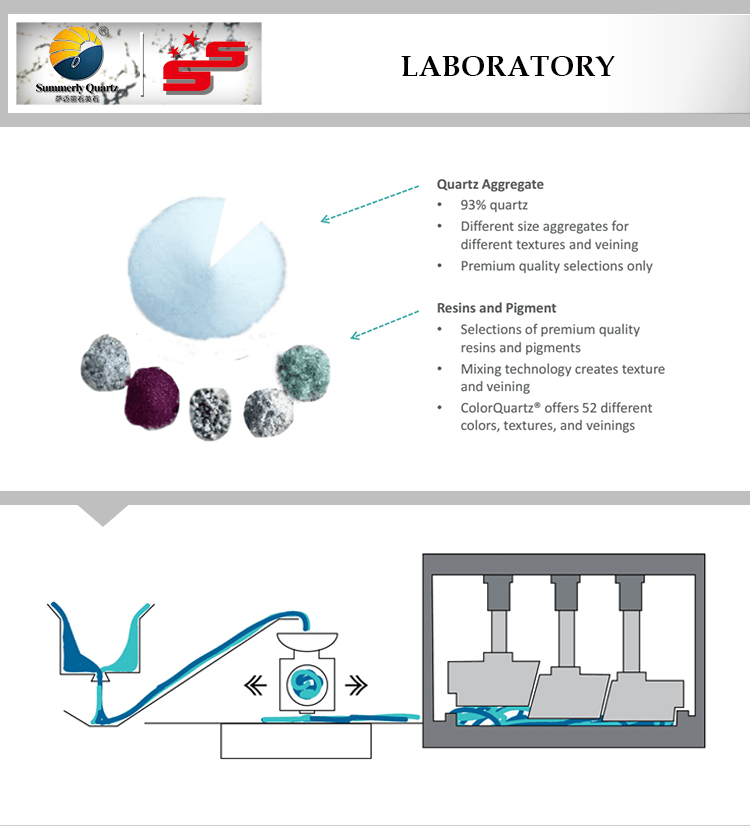