Iteml No:
|
SS2809-Pure-Rosy
|
Color:
|
Rosy
|
Standard size:
|
3000x1400mm,3000x1600mm, 3200x1400mm,etc.
|
Thickness:
|
15mm; 18mm; 20mm; 30mm,etc
|
Glossiness:
|
70-90
|
Surface Flatness
|
<0.50mm
|
Compress Strength
|
260 MPa
|
Packing:
|
In Strong Fumigated Wooden Crate. ( or customized )
|
Quality Control:
|
Thickness tolerance for tile:+-0.5mm;+-1mm. All products are checked by experienced QC then packed.
|
Payment Terms
|
T/T, L/C at sight
|
Usage:
|
Vanity tops,shower stalls, tub surrounds,kitchen tops, worktops, Bar top,etc.
|
Sample:
|
It Is Free and Available Upon Requests
|
Quartz countertop is not only a great option because of its timeless looks, but especially because of the functionality of the hard rock material. The Quartz surface is basically 93% of quartz mixed with resin, making the surface extremely hard. This basically means that it is also very resistant to chips, scratches and stains. In an area like a kitchen or bathroom, bar top with spills and risk of permanent stains, this material will fit like a glove. If you are wanting to keep your kitchen countertops looking their very best than a tiny bit of maintenance is the answer. This is important no matter which material you choose. Looking after your quartz countertop is fast and simple. To clean your countertop, rinse it with warm water and a mild detergent, and it will be as good as new.
Quartz can have the appearance of other materials, like marble or quartz, while giving additional qualities. The imitations are so accurate, only the experts will know a difference between a marble looking quartz and real marble. Quartz countertops have consistent color patterns, as opposed to natural stones having large color variation in them. By practicing standard care, your finish will look remarkable throughout your countertop’s lifetime.
Production Engineering:
1. The process begin with a rigorous inspection of raw materials.
2. Feeding natural quartz raw material and polymer resins and inorganic pigments in to mixers and blending them together.
3. After stirring the mixture, then pouring them into a mold and form them into slab size.
4. Pressing: Then the slab is compacted by a special vacuum and vibration process at pressure machine.
5. The slab then moved to the curing kiln and heated for a period time which give them ultimate strength and solidity.
6. Trimming edges, leveling , thicknessing and polishing surface to perfect finished.
7.Finally, the quartz stone slabs passed through quality inspection and packed with a plastic film.
Packing wooden crate (slab) wooden box (tiles/ countertop)
Packing For Slab:
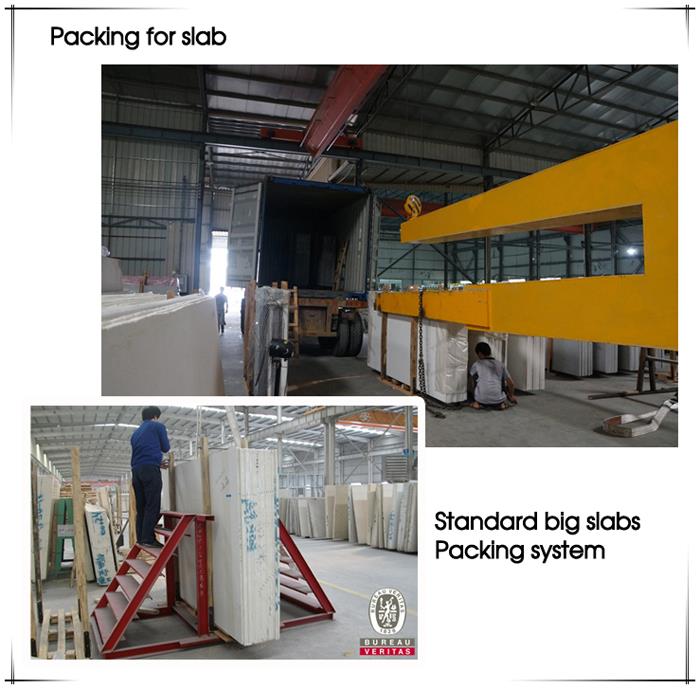