Products Type
|
Artificial Quartz Stone
|
Model No
|
SS6701 Kashmir Venato
|
Color
|
White
|
Slab Size
|
3000 X 1400mm, 3000 X 1600mm, 3200 X 1600mm, 3200 x 1650mm, etc.
|
Thickness
|
15mm, 18mm, 20mm, 30mm.
|
Compressive Strength
|
>200 Mpa
|
Flatness
|
<0.1 mm
|
Flexural Strength
|
25~35 Mpa
|
Application
|
kitchen Counter tops, bathroom vanity top, wall tile, flooring tile ,etc.
|
Quality
|
Control by Our Experienced QC Team
|
Package
|
plastic inside + strong seaworthy wooden bundle outside
|
Main Market
|
North America, South America, Europe, Australia, The Middle East, Africa and Southeast Asia,etc.
|
Quartz is undoubtedly one of the best countertop options on the market for many reasons, not the least of which are color/pattern options, durability, hygiene and its sustainable origins and manufacturing processes. For anyone who wants a granite or marble countertop, it is worth investigating quartz counters as an alternative. Quartz has much of the chaotic appearance as does natural stone, without stone's unpredictability. Whether you have a family home or live alone, Quartz is one fit for all. Quartz can be used in all high traffic areas and withstand high volumes of usage.
The porous composition of natural stones can lead to cracks and allow bacteria to grow if not properly maintained. This is not a problem though when you choose Quartz. Quartz surface requires zero upkeep and never requires top coat applications. It is porous-free which means that your surface can remain virtually bacteria free by simply wiping it clean. Furthermore, as it will never soak up any liquid this is perfect for being used in the kitchen or bathroom areas.
Production Engineering:
1. The process begin with a rigorous inspection of raw materials.
2. Feeding natural quartz raw material and polymer resins and inorganic pigments in to mixers and blending them together.
3. After stirring the mixture, then pouring them into a mold and form them into slab size.
4. Pressing: Then the slab is compacted by a special vacuum and vibration process at pressure machine.
5. The slab then moved to the curing kiln and heated for a period time which give them ultimate strength and solidity.
6. Trimming edges, leveling , thicknessing and polishing surface to perfect finished.
7.Finally, the quartz stone slabs passed through quality inspection and packed with a plastic film.
Packing wooden crate (slab) wooden box (tiles/ countertop)
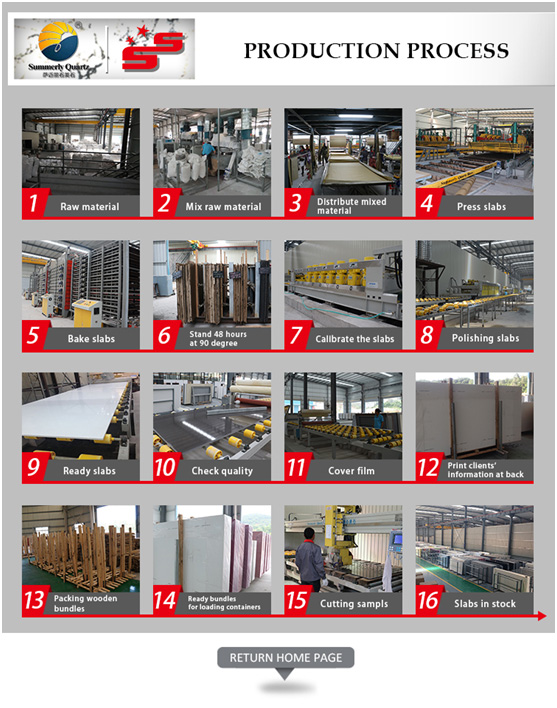