Item No
|
SS3868 South Africa Dark Brown
|
Color
|
Dark Brown
|
Product
|
Big slab, Countertop, Table top, Vanity top,
|
Thickness
|
12 mm, 15 mm, 18 mm, 20 mm, 30 mm
or custom- made is available
|
Size
|
3000x1400mm,3000x1600mm, 3200x1400mm, 3200x1600mm etc.
|
Thickness
|
12 mm, 15 mm, 18 mm, 20 mm, 30 mm,etc.
|
Finishing
|
Polished, Honed, etc
|
Density
|
2364 Kg/M3
|
Mohs′ Hardness
|
7
|
Tone & Figure
|
< Consistent
|
Quality Control
|
Confirm Every Details Before Make the Rough Production
Thickness tolerance: ±0.5mm, ±1mm, 90 degree up polished
All products were checked by experienced QC before packed
|
Packing
|
Plastic inside strong seaworthy
wooden bundle outside
|
Artificial
Quartz is made from over 93% of quartz. The natural quartz in Artificial Quartz
delivers distinctive depth, brilliant clarity, glimmering radiance and a cool,
solid feel unique to natural stone.Quartz has begun to top the lists of
countertop options for designers and homeowners alike. Anyone that wants a
durable, low maintenance, and attractive countertop material is likely to
consider quartz. Quartz is a manufactured surface that is made by mixing 93%
ground natural quartz with 7% polymer resins. The result is a material that
still looks natural. If you are remodeling a bathroom or considering using
quartz for your kitchen countertops, quartz is good choice .
Quartz
doesn't just look great, but it can be easy to clean as well. Whether it's a big
spill or everyday dust, there's no trick to cleaning this smooth surface.
Simple soap and water usually does the trick. Material that has hardened
on the surface can be removed with a gentle cleansing scrub. Abrasive scrubs
and cleansers that contain bleach and harsh chemicals should be avoided, as
these can dull the surface and break down the bonds within the quartz stone.
Application:
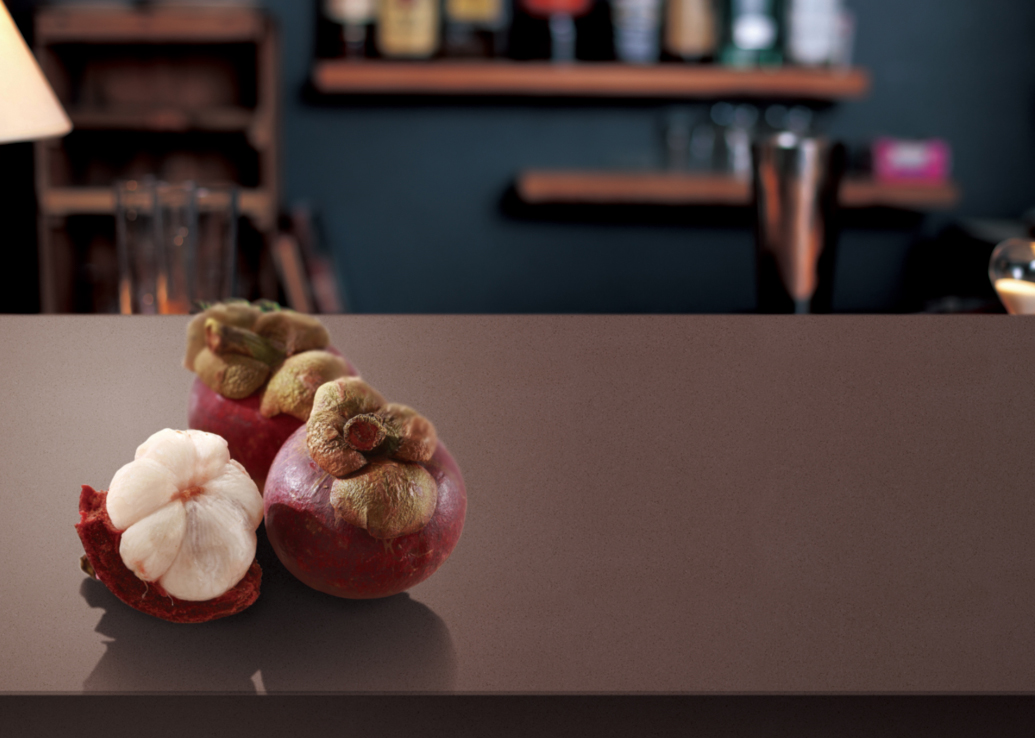
Production Engineering:
1. The process begin with a rigorous inspection of raw
materials.
2. Feeding natural quartz raw material and polymer resins
and inorganic pigments in to mixers and blending them together.
3. After stirring the mixture, then pouring them into a
mold and form them into slab size.
4. Pressing: Then the slab is compacted by a special
vacuum and vibration process at pressure machine.
5. The slab then moved to the curing kiln and heated for
a period time which give them ultimate strength and solidity.
6. Trimming edges, leveling , thicknessing and polishing
surface to perfect finished.
7.Finally, the quartz stone slabs passed through quality
inspection and packed with a plastic film.
Packing wooden crate (slab) wooden box (tiles/ countertop)
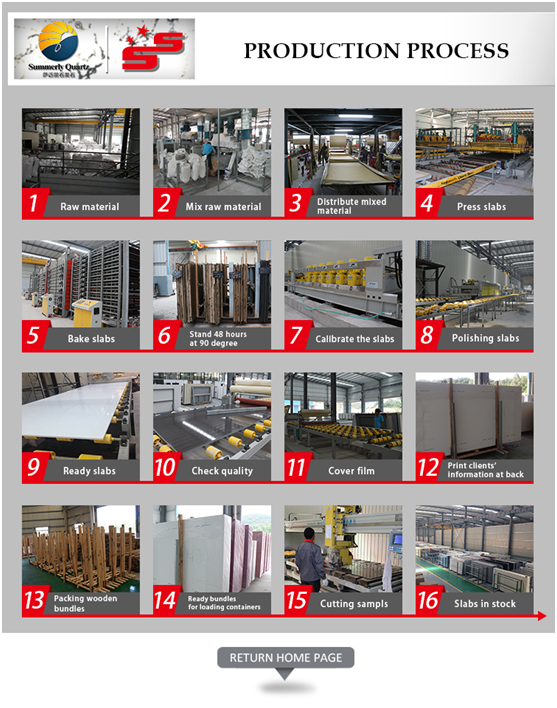