Name
|
Artificial Quartz Stone
|
Model No
|
SS6312
Snow Vein
|
Sizes
|
3000x1400mm,3000x1600mm, 3200x1400mm,etc.
|
Thickness
|
12mm,
15mm, 18mm, 20mm, 30mm.etc.
|
Thickness Difference
|
1.0mm
|
Surface finishes
|
polished, honed, or others
|
Hardness
|
7 Mohs
|
Temperature Resistance
|
≥300ºC
|
Quality control
|
Color difference control,Safe packing,
Thickness tolerance: /-1mm
All products are checked by experienced QC piece by piece and then pack
|
Packing
|
Strong
wooden crates with fumigation.
|
Delivery
|
T/T, irrevocable L/C at sight, Western Union.
|
Usage
|
kitchen countertop, bathroom tops, washing
room tops, window sills top,etc.
|
Quartz countertop
offers the natural beauty of quartz with up to six times the strength and
durability of granite. Approximately 93 percent of Quartz countertop is mined
quartz crystals, one of nature’s hardest materials. The quartz is combined with
high-quality polyester resins and pigments producing a engineered stone without
the high-maintenance while making it resistant to heat, scratches, and stains.
The hard surface of
Quartz is non-porous and very resistant to staining, even better than
marble. Quartz counters can resist oil,
coffee, wine, juice and most other common kitchen spills. However, when
cooking, use trivets or heating pads to guard the countertop surface against
direct exposure to hot cookware or coffee pots. Although quartz is resistant to
stains, it is best to wipe up spills immediately to prevent possible stains.
When chopping vegetables, slicing bread or preparing other foods with sharp
utensils, use a cutting board to prevent scratches.
Production Engineering:
1. The process begin with a rigorous
inspection of raw materials.
2. Feeding natural quartz raw material and
polymer resins and inorganic pigments in to mixers and blending them together.
3. After stirring the mixture, then pouring
them into a mold and form them into slab size.
4. Pressing: Then the slab is compacted by a
special vacuum and vibration process at pressure machine.
5. The slab then moved to the curing kiln and
heated for a period time which give them ultimate strength and solidity.
6. Trimming edges, leveling , thicknessing
and polishing surface to perfect finished.
7.Finally, the quartz stone slabs passed
through quality inspection and packed with a plastic film.
Packing wooden
crate (slab) wooden box (tiles/
countertop)
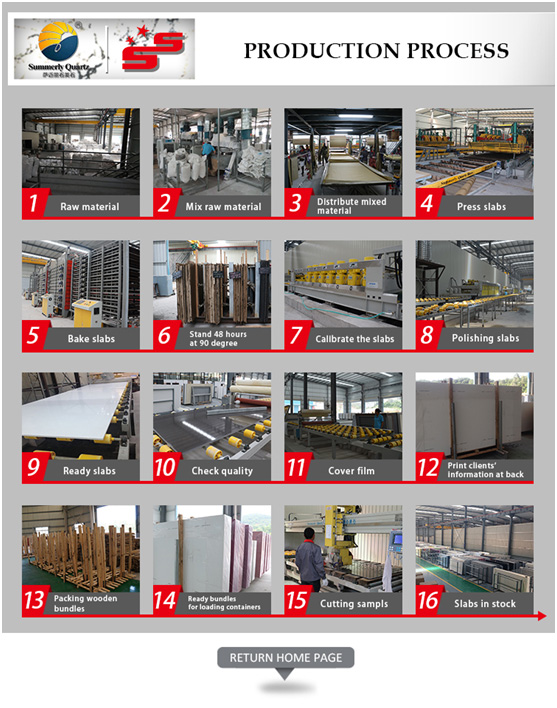