Product name
|
Calacatta V007
|
Size
|
3000x1400mm,3000x1600mm, 3200x1400mm, 3200x1600mm etc.
|
Thickness
|
20mm,30mm
|
Surface Finishing
|
Polished, Honed, etc.
|
Flatness
|
<0.1mm
|
Flexural Strength
|
25~35 Mpa
|
Tone & Figure
|
Consistent
|
Sample Request
|
Free Sample with Freight by Customer
|
Quality Control:
|
Safe packing
Color differece control
Thickness tolerance: /-1mm
All products checked by experienced QC pieces by pieces and then pack
|
Package
|
Quartz Stone Slabs packed in wooden frames suitable for ocean shipment
|
The countertop is an essential component of the kitchen or bathroom. It is where all the action takes place. But more than that, the countertop is the foundation of home décor when doing a home renovation. It bares the burden of setting the tone and feel of the space. Quartz countertops are manufactured, so,the color and pattern possibilities are endless, including options that are almost identical to granite or marble. One of the largest benefits of quartz surfaces is they tend to scratch resistant, stain proof to a high degree. making them very easy to maintain. Its non-porous quality also makes it highly resistant to mold and bacteria contamination.
Quartz is heat resistant, but not completely heat proof.You can’t do with quartz is sit a hot pot directly on the surface. It can melt the reasons and cause damage. Typically a coffee mug or warm plate is fine, but a hot pot or pan directly from the cooktop or oven is not. It is best to user a trivet or hot pad for any hot items you place on the countertop. But overall, quartz is extremely durable, scratch resistant, and stain resistant. The perfect combination of strength, low maintenance, and beauty is possible with the selection of engineered stone countertops. Quartz countertops are considered environmentally-friendly and adaptable to any room in the home.
Application:
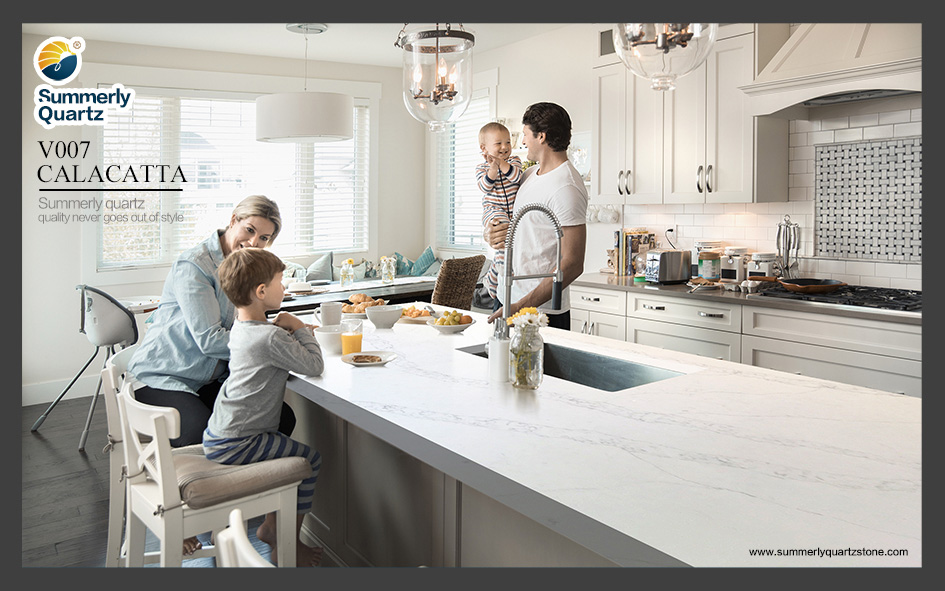
The Production Process:
1. The process begins with a strict inspection of raw materials.
2. The natural quartz raw material and polymer resins and inorganic pigments are put into the mixers and mix together.
3. After mixing, pour them into a mold and form them into slab size.
4. Pressing: Then the slab is compacted by a special vacuum and vibration process at pressure machine.
5. Then the slab is moved to the curing kiln and heated for a period time to make their final strenth and srurdiness.
6. Cut edges, flat , thicknessing and polishing surface to perfect finished.
7. Finally, through quality inspection and plastic film packaging.
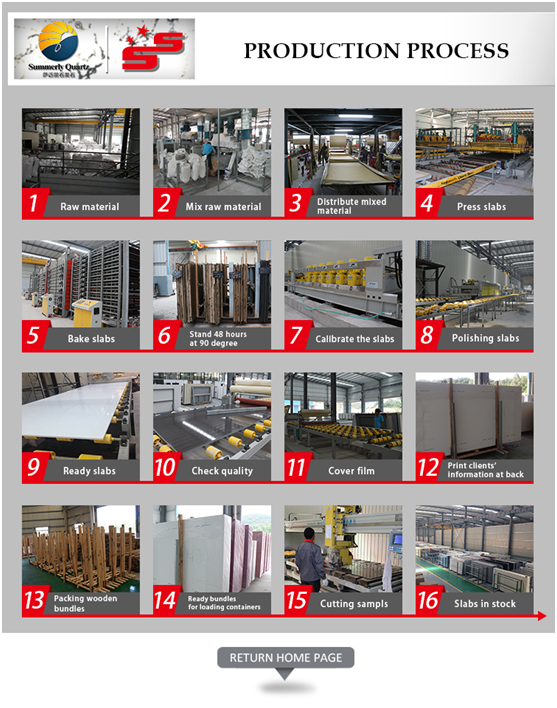