Roller – Ultrasonic Detection Machine(Duel Channel)【Cylinder / Tapered】
Roller Ultrasonic Testing Machine is mainly used to detect a variety of internal defects of cylindrical workpiece, such as: weld, crack, inclusion, folding, porosity, sand, etc. The workpiece is transported and pushed to the loading station by a feeding conveyor, then a loading manipulator picks up the workpiece and sends it to the double-roller conveying self-rotating mechanism. The workpiece in the double-roller conveying self-rotating mechanism keeps moving forward and starts to rotate by itself until it passes the ultrasonic detection probe and automatically be transported to the blanking position. The unloading manipulator will pick up the workpiece and send it to the discharging conveyor. If the workpiece is a NG products, the elimination mechanism will move it to the NG box. Unqualified products can be classified into 2 kinds according to the customer request, such as surface defect NG and internal defect NG, and qualified product will be released to the next process. The equipment is double channel detection to improve the efficiency.
Technical Parameter:
Detect objects:Ultrasonic,Ø20-40/Ø40-60
Air source:0.4Mpa≦P≦0.7Mpa
Power:220V/50Hz
Size:2300×1350×2200mm
Weight:1100KG
Gross Power:≈2.0KW
Equipment General Drawing:
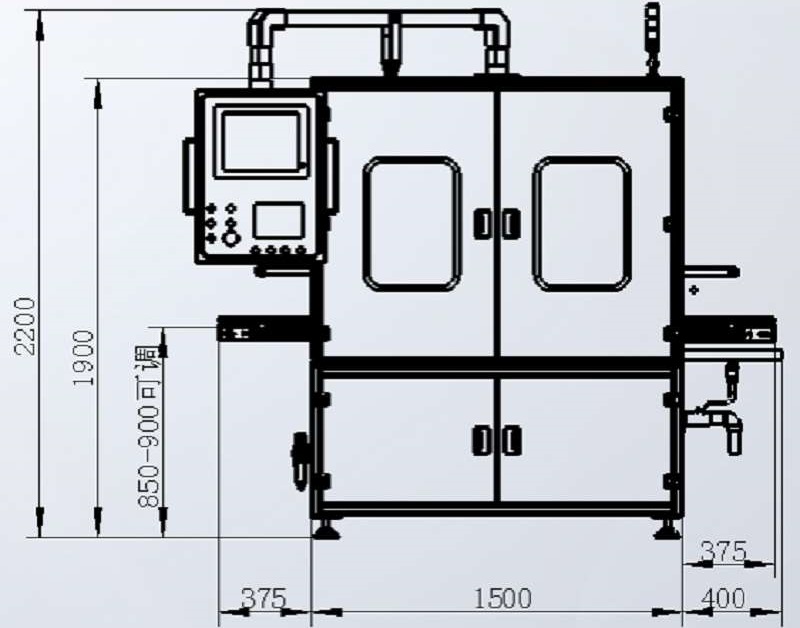
Characteristic:
Controlled by PLC, machine count Number of products tested, unqualified products & Failure rate automatically to help customers improving the production process in the production and the pass rate.