Composition:
|
93 % pure quartz crystal, with 7 % of resins, color pigments and others .
|
Model No:
|
SS5010 Sunset
|
Available Size:
|
3000x1400mm,3000x1600mm,3200x1600mm,etc.
|
Thickness::
|
15mm,18mm,20mm,30mm,etc.
|
Temperature Resistance:
|
≥300ºC
|
Application :
|
Countertops, worktops, table tops, island tops, vanity tops, bench tops, bar tops, backsplashes, etc.
|
Package:
|
In Strong Fumigated Wooden Crate. ( or customized )
|
Payment Terms:
|
T/T, L/C at sight
|
MOQ:
|
100 Square meters
|
Quartz countertop is a man-made product, this material can be tinted and shaped in a wide variety of ways. Unique colors, edge treatments, inlays and other style accents add to the aesthetic appeal of this product. In general, engineered stone is less expensive than naturally sourced materials after installation, sealing and maintenance are considered. Quartz is an engineered stone. Engineered stone is a composite material made of crushed stone (quartz) bound together by an adhesive. The color and patterns can be altered by using different pigments and materials during the engineering process. Quartz can be designed to mimic other natural stones, such as granite or marble.
With quartz, porosity isn’t an issue at all. With a nonporous surface, homeowners don’t have to worry about water or liquid substances seeping through and forming stains. Quartz countertops can generally handle heat better than natural stone.But placing hot pans and baking sheets on them is a gamble because you never know when thermal shock will cause natural stone to crack. Even though quartz is more heat resistant than natural stone, it’s better to not place hot items directly on top because constantly doing so may result in discoloration.
Production Engineering:
1. The process begin with a rigorous inspection of raw materials.
2. Feeding natural quartz raw material and polymer resins and inorganic pigments in to mixers and blending them together.
3. After stirring the mixture, then pouring them into a mold and form them into slab size.
4. Pressing: Then the slab is compacted by a special vacuum and vibration process at pressure machine.
5. The slab then moved to the curing kiln and heated for a period time which give them ultimate strength and solidity.
6. Trimming edges, leveling , thicknessing and polishing surface to perfect finished.
7.Finally, the quartz stone slabs passed through quality inspection and packed with a plastic film.
Packing wooden crate (slab) wooden box (tiles/ countertop)
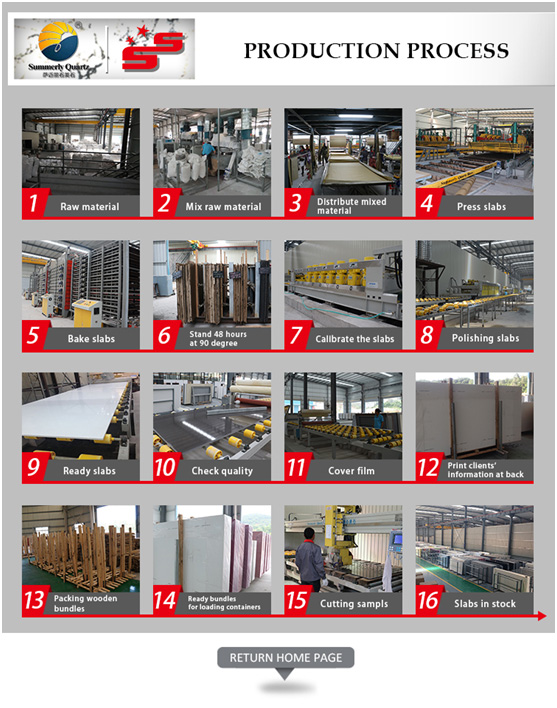