M800 series high performance EtherCat servo drives
M800 series is a new generation of high-performance EtherCat servo drives independently developed by MT. It reduces the size, improves product performance and power density, and makes it perfect.
M800 adopts the unique single-axis and dual-axis modular design. Customers can choose their own power (0.05 ~ 4.5kw) and freely combine them into servo drives with any number of axes from 1 to 10. The highly integrated structure greatly reduces the installation size and simplifies On-site wiring; EtherCAT bus communication method, making the product communication cycle as short as 250us; seamless connection with master stations such as Beckhoff TwinCAT platform, CodeSYS platform, Omron, Keyence, Trio, Baoyuan, etc .; only one The root network cable can realize multi-axis joint control, which greatly reduces user wiring costs and improves system reliability.
M800 series products have been widely used in many industries with excellent system characteristics, excellent product quality, novel product forms and other characteristics, and have won unanimous praise from customers. Industrial robot industry (SCARA, Delta, 6 joints, 4 joints), mechanical arm industry, 3C industry (grinding, testing and other equipment), lithium battery industry (winding equipment, die cutting equipment, lamination equipment, etc.), woodworking industry (open Feeders, 6-sided drills, etc.), packaging, winding, semiconductor, CNC, engraving, engraving and milling, and many other benchmarking companies in the multi-axis servo drive industry have established close cooperative relationships with MT.
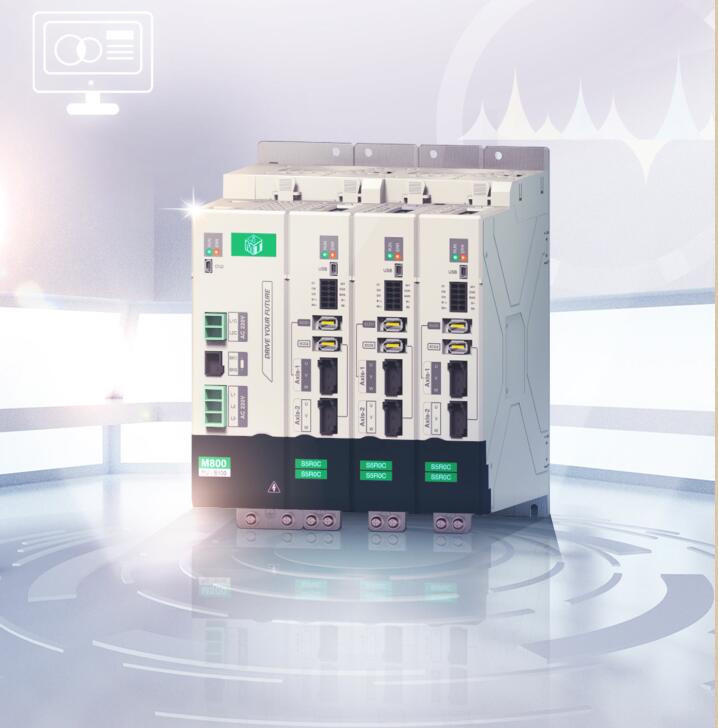
M800
Specification:
Function
|
Specifications
|
Basic Function
|
Power Supply
|
Single-phase / three-phase AC220V
(-15% ~ + 10%) 50 / 60Hz
Note: When the sum of the rated
output currents of multiple axes exceeds 20A, three-phase AC220V power supply
is recommended
|
Control Method
|
Position, speed mode, torque mode,
mixed control mode.
|
Max Toque
|
Max 300%
|
Output frequency
|
0~600Hz
|
Current loop period
|
62.5us
|
Overload
|
150% rated current output 100s; 300%
rated current output 3s
|
Protection
|
Protect Funtion
|
Driver overload, overcurrent, short circuit, overvoltage,
undervoltage, overheating, output failure, etc.
|
Bus
|
EtherCAT
|
Dedicated EtherCAT, standard DS402
synchronization cycle 250us ~ 32ms
|
M800 series product feature:
50% reduction in volume and wiring time
Compared
with the traditional single servo, the installation volume of M800 / M820 is
greatly reduced, among which 4 axes save 35% ~ 40%, 6 axes save 45% ~ 50%, 8
axes save 50% -55%, and 10 axes save 55%- 60%; (Take 750w power as an example,
1kw ~ 3kw power saves more volume)
Multi-axis
modular servo managed by centralized power module, eliminating the power supply
line, auxiliary power line, control harness, and brake power of each servo
axis, greatly reducing the workload of customers' field wiring, improving the
efficiency of electrical enclosures, and saving Installation costs.
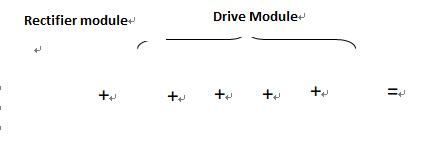
30% energy savings
MT's unique patented connection between drive modules allows easy expansion of any number of axes. Through the common DC bus electrical topology, the energy generated by the brake shaft is supplied to other shafts to improve the efficiency of electric energy utilization. Compared with traditional single servo, it can reduce energy consumption by 30% on average.
250us communication cycle
EtherCAT is a bus communication method based on industrial Ethernet technology and using distributed clock synchronization. It is also the most mainstream industrial real-time bus communication technology:
1. Transmission speed can reach 100Mbps (full duplex);
2. The shortest communication period can reach 250us, reaching the first-class level in the industry;
3. High-precision distributed clock, accurate synchronization (<1us);
4. Supports standard DS402 and Motorola's custom EtherCAT protocol (high reliability);
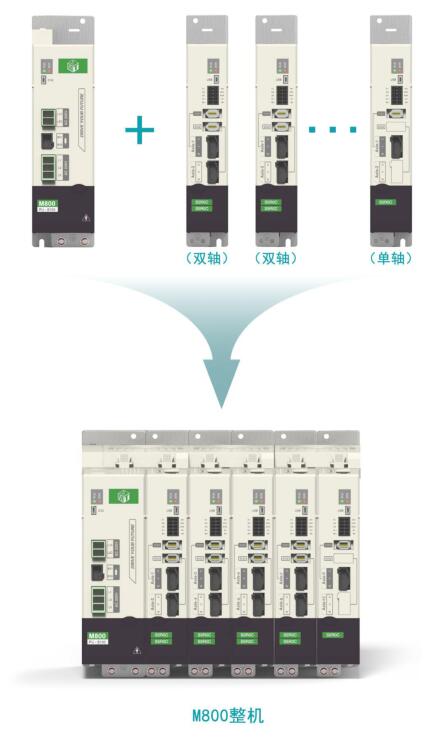
250us communication cycle
EtherCAT is a bus communication method based on industrial Ethernet technology and using distributed clock synchronization. It is also the most mainstream industrial real-time bus communication technology:
1. Transmission speed can reach 100Mbps (full duplex);
2. The shortest communication period can reach 250us, reaching the first-class level in the industry;
3. High-precision distributed clock, accurate synchronization (<1us);
4. Supports standard DS402 and Motorola's custom EtherCAT protocol (high reliability);
3.2kHz response speed
3.2kHz maximum speed loop bandwidth, 16kHz current loop refresh cycle, specially designed for high-speed, high-precision motion control scene design, greatly reducing system response time, improving equipment performance and efficiency.
Minimal, flexible and efficient
Industry gain-free adjustment: High-performance servo motor control algorithm, which maximizes in robots, manipulators, woodworking machinery, 3C industry
Parameters are exempt from adjustment.
Minimalist (three open debugging modes): EtherCAT master debugging (open SDO + cross-platform monitoring kernel),
USB host computer software, remote keypad. M800 / M820 series products open all SDOs, which can be completely controlled by the host computer.
In the test, the user EtherCAT master station can monitor the parameters of the servo axes in real time through the embedded Motorola cross-platform kernel;
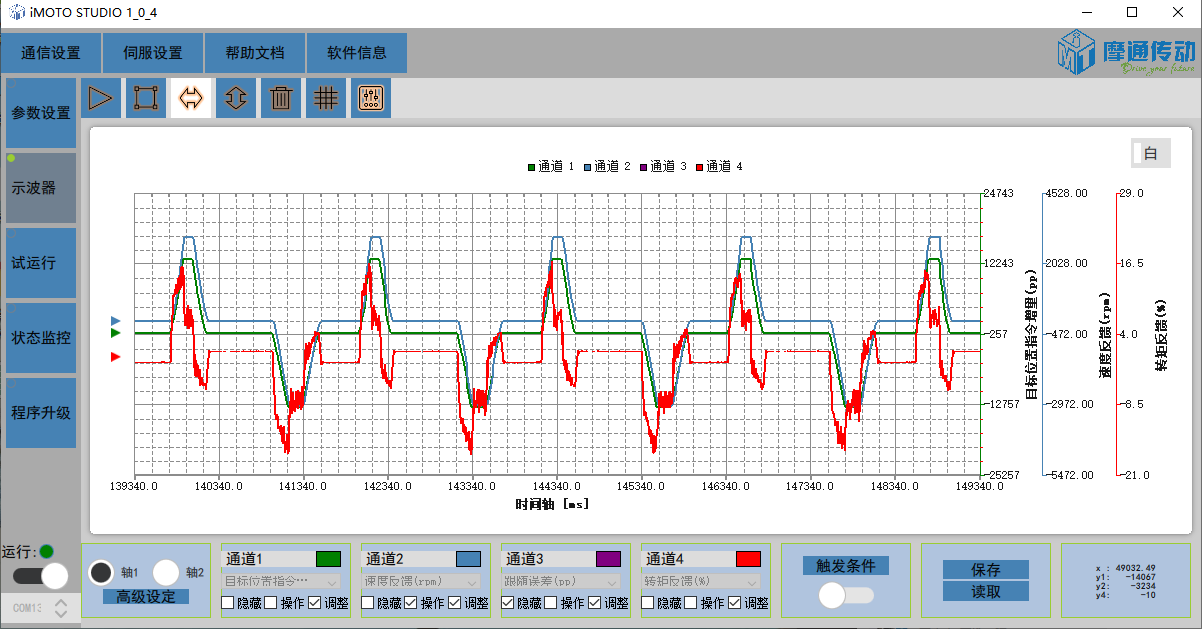
M800 series servo drive models
M800/M820
|
T020*
|
T015*
|
S015
|
S8R0
|
S5R0
|
S2R0
|
Continuous output current [A] rms
|
20.0
|
15.0
|
15.0
|
8.0
|
5.0
|
2.0
|
Instant maximum current [A] rms
|
60.0
|
45.0
|
45.0
|
24.0
|
20
|
6.0
|
Main circuit power
|
3 phase AC 380V 50/60Hz
|
single/3 phase AC 220V (-15%~+10%),50/60Hz
|
Overvoltage Level
|
III
|
Note:
The 380V model is a single servo drive.
M800 & M820 series servo driver installation
size (2 ~ 10 axis)
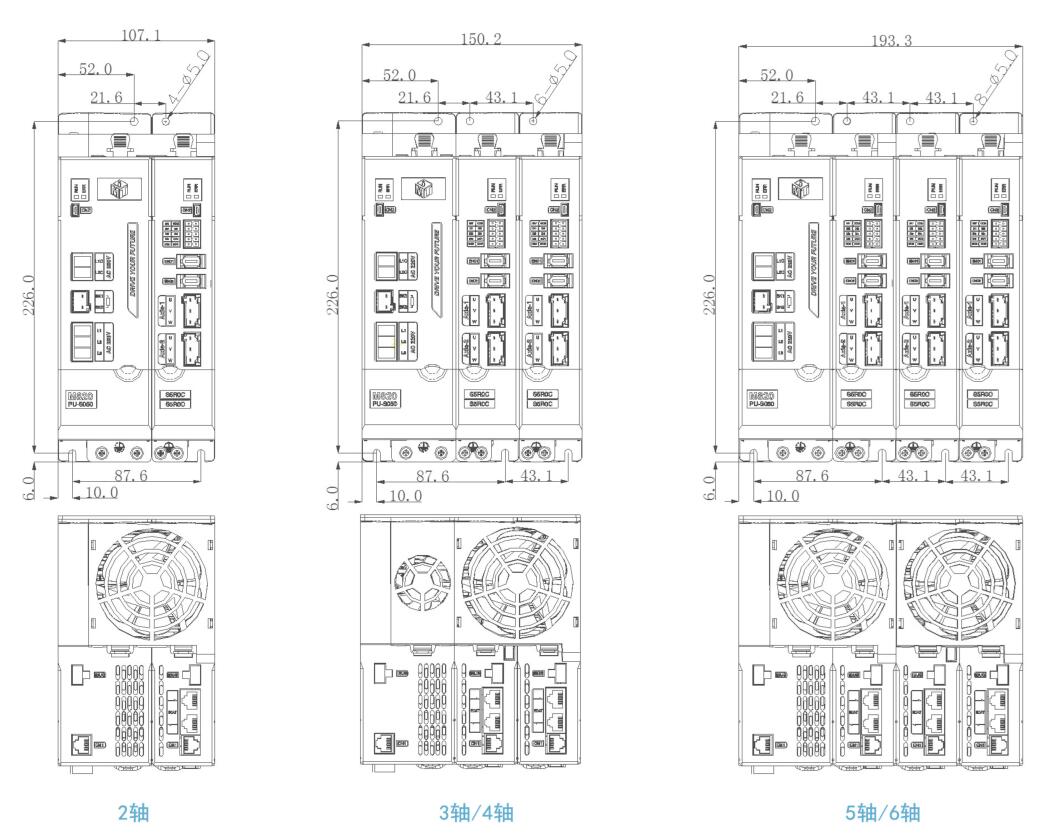
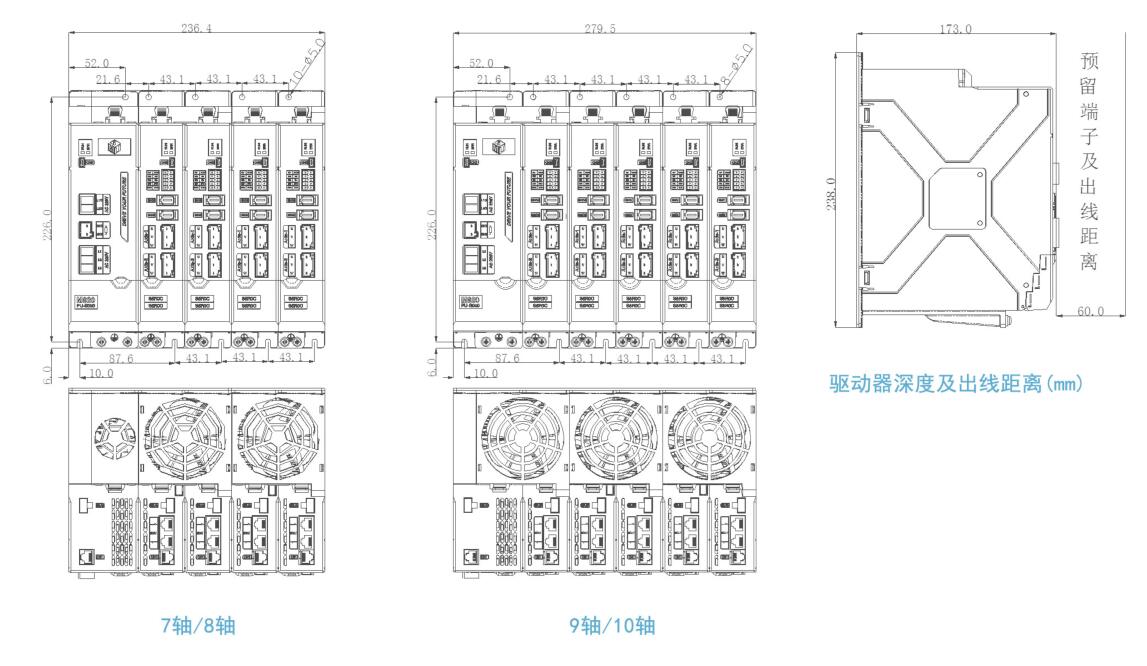