Product Name:
|
SS6311
Tiny Carara
|
Color:
|
White
|
size:
|
3000 X 1400mm, 3000 X 1600mm, 3200 X 1600mm, 3200 x
1650mm, etc.
|
Thickness:
|
15mm, 18mm, 20mm, 25mm, 30mm
|
Tone & Figure:
|
Consistent
|
Samples:
|
Free Small Quartz Sample
|
Package:
|
packed with strong wooden crates and foam, film inside
|
Usage:
|
kitchen worktop, bathroom vanity top, washing room
tops, dressing top, etc.
|
Service:
|
We can offer high quality, competitive price and swift
delivery
|
Payment Terms:
|
Usally T/T (30% deposit / 70% before loading ), 100%
L/C at sight.
|
Quartz, otherwise known as engineered
stone, is a stone made up of around 93% natural quartz and 7% resins. Various
colors and materials can be mixed into the stone to give a unique color and
pattern to the finished product. Natural
stone is unique, which means that each slab is different from the next. In
contrast, quartz offers uniformity in terms of both color and pattern, so you
can be sure that the countertop you select quartz is the same as the slab you
will get.
Our countertop collection comes in a
variety. We have many different patterns, colors, and textures for you to
select from. Quartz countertops are the leading material that most homeowners
choose because of its outstanding qualities which include durability and easy
maintenance.
Quartz is impervious to bacteria and other
microorganisms, and easily wipes clean for a hygienic surface you can trust.
Being non-porous, they are the best stain-resistant material you can choose,
resisting even wine and oil, juice and coffee. Even if you do spill something
on the counter you will soon find how easy it is to clean its’ surface.
Cleaning is also the only maintenance you will ever need to provide.
The Production Process:
1.
The process begins with a strict inspection of raw materials.
2.
The natural quartz raw material and polymer resins and inorganic pigments are
put into the mixers and mix together.
3.
After mixing, pour them into a mold and form them into slab size.
4.
Pressing: Then the slab is compacted by a special vacuum and vibration process
at pressure machine.
5.
Then the slab is moved to the curing kiln and heated for a period time to make
their final strenth and srurdiness.
6.
Cut edges, flat , thicknessing and polishing surface to perfect finished.
7.
Finally, through quality inspection and plastic film packaging.
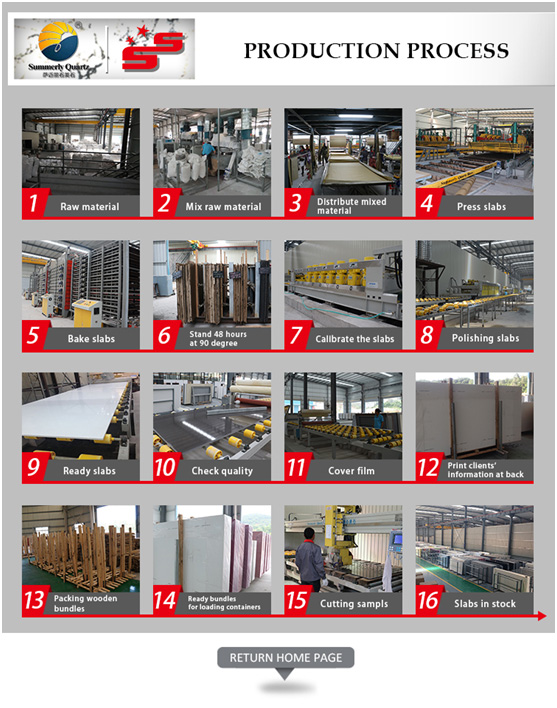
Product Inspection:
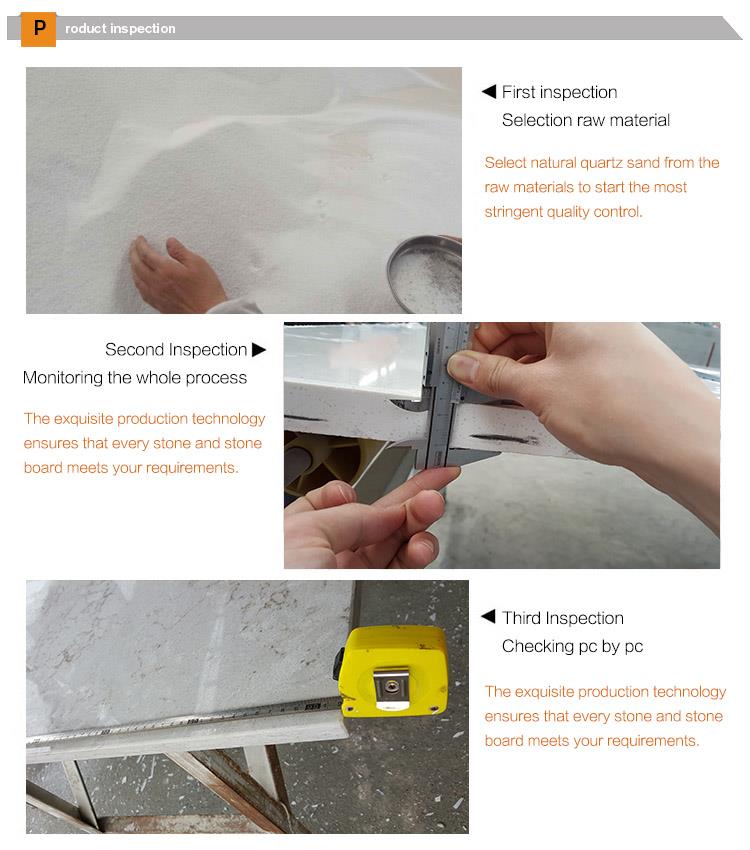