Item No
|
SS2803 Pure Yellow
|
Color
|
Yellow
|
Composition
|
93 % pure quartz crystal, with 7 % of resins, color pigments and others .
|
Slab Size(mm)
|
3000x1400mm,3000x1600mm, 3200x1400mm, 3200x1600mm etc.
|
Thickness
|
12mm, 15mm, 18mm, 20mm, 30mm,etc.
|
Customzied Color & Size
|
Acceptable
|
Glossiness
|
More Than 50 Degrees
|
Quality Control
|
Size tolerance: ±0.5mm ~ ±1mm
Glossiness: 90 degree polished or up
Strict QC control system ensure every piece is strictly checked before packing
|
Usage
|
kitchen countertop, vanity top, table top, window, and other.
|
Service
|
We can offer high quality, competitive price and swift delivery
|
Payment
|
T/T(30% deposit), irrevocable L/C at sight
|
Quartz, also called engineered stone. It is one of the hardest minerals on earth, thus when used as a countertop option in homes, it is arguably the most durable choice. Unlike other mined natural stone slabs, quartz is produced in a factory. Quartz countertops are easy to love and quite beautiful. They add a certain element of luxury to any space with their gorgeous reflective charm. Quartz is another well-loved countertop choice. Quartz is composed of natural quartz crystals, making one of the most beautiful and durable countertop selections for your home. Plus, its beauty is matched by its durability, making it a great choice for homeowners who love to cook.
It is beneficial to routinely clean your quartz with non-abrasive granite cleaning pads and stone-safe cleaning products. However, quartz is a low maintenance stone due to its nonporous characteristics.From time to time, you can do the deep cleaning, to remove all the buildup and residue from everyday use. You can do the deeper cleaning with professional cleaning products or just mix some vinegar and water, or you can use the glass cleaner. Both will leave your surfaces very clean and super shiny.
The Production Process:
1. The process begins with a strict inspection of raw materials.
2. The natural quartz raw material and polymer resins and inorganic pigments are put into the mixers and mix together.
3. After mixing, pour them into a mold and form them into slab size.
4. Pressing: Then the slab is compacted by a special vacuum and vibration process at pressure machine.
5. Then the slab is moved to the curing kiln and heated for a period time to make their final strenth and srurdiness.
6. Cut edges, flat , thicknessing and polishing surface to perfect finished.
7. Finally, through quality inspection and plastic film packaging
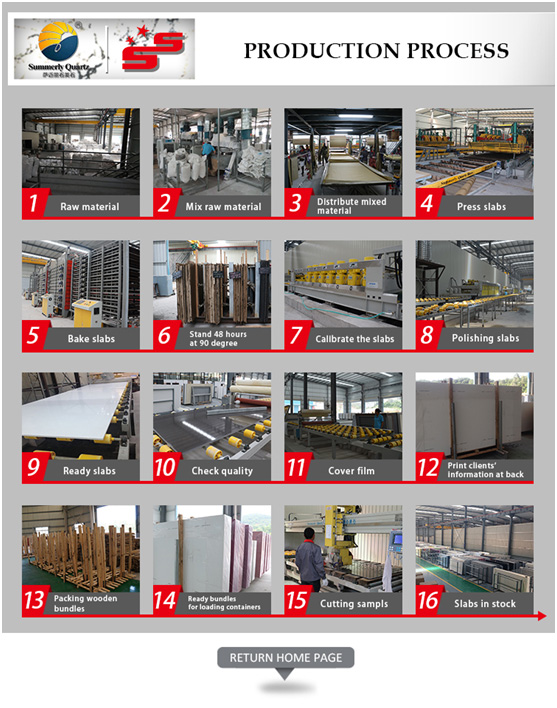